SKD production line / assembly line solution for sedans and SUVs
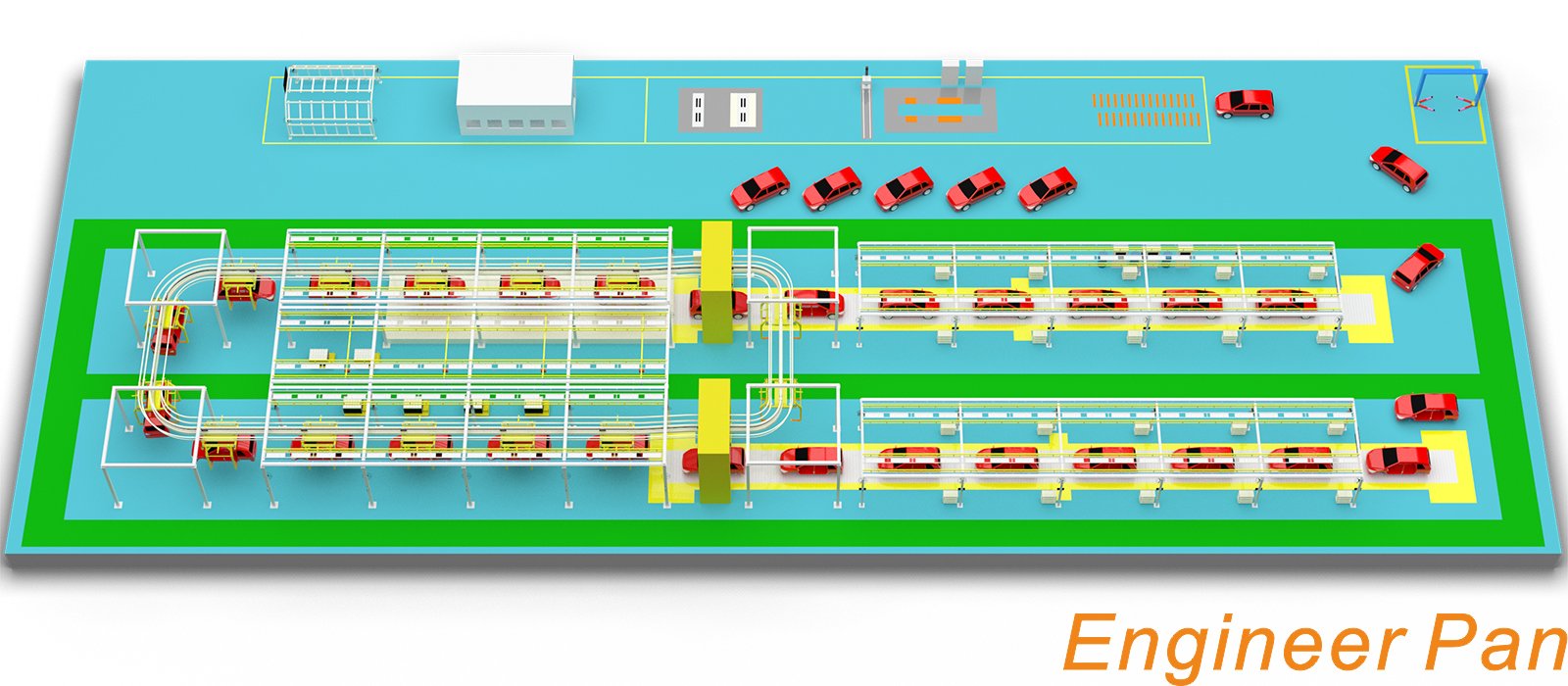
This is a compact SKD production line specifically designed for unibody vehicle structures, suitable for sedans and SUVs. It integrates several key processes including pre-assembly, logistics coordination, final assembly, inspection equipment, management information systems, and safety facilities, all aimed at achieving an efficient and flexible production process. This setup is designed to meet the diverse market demands for sedans and SUVs, while reducing transportation costs and enhancing assembly efficiency at the destination.
SKD Production line suitable
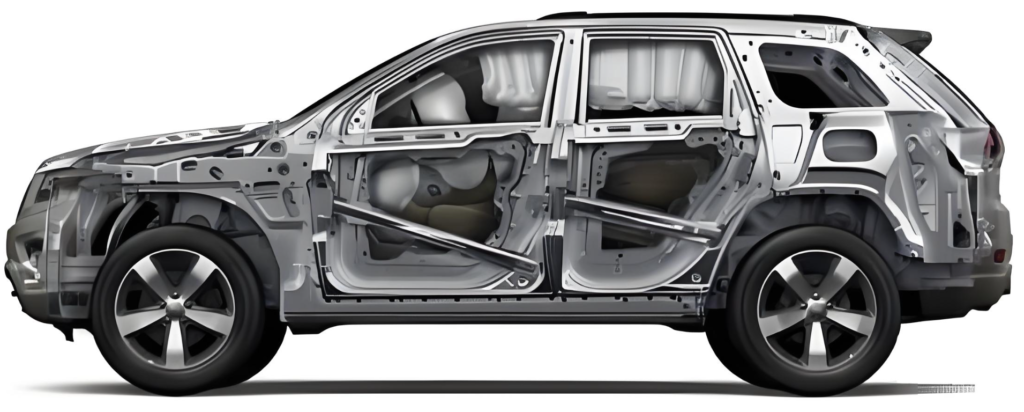
The unibody construction is widely applied to a variety of car models, including sedans, SUVs, MPVs, compact cars, electric vehicles, and some luxury and sports cars. This design integrates the body and chassis into one unit, offering improved handling, comfort, and space efficiency, while also contributing to vehicle weight reduction and fuel economy. It is a common body structure in modern automotive design.
Assembly line installation workshop size requirements
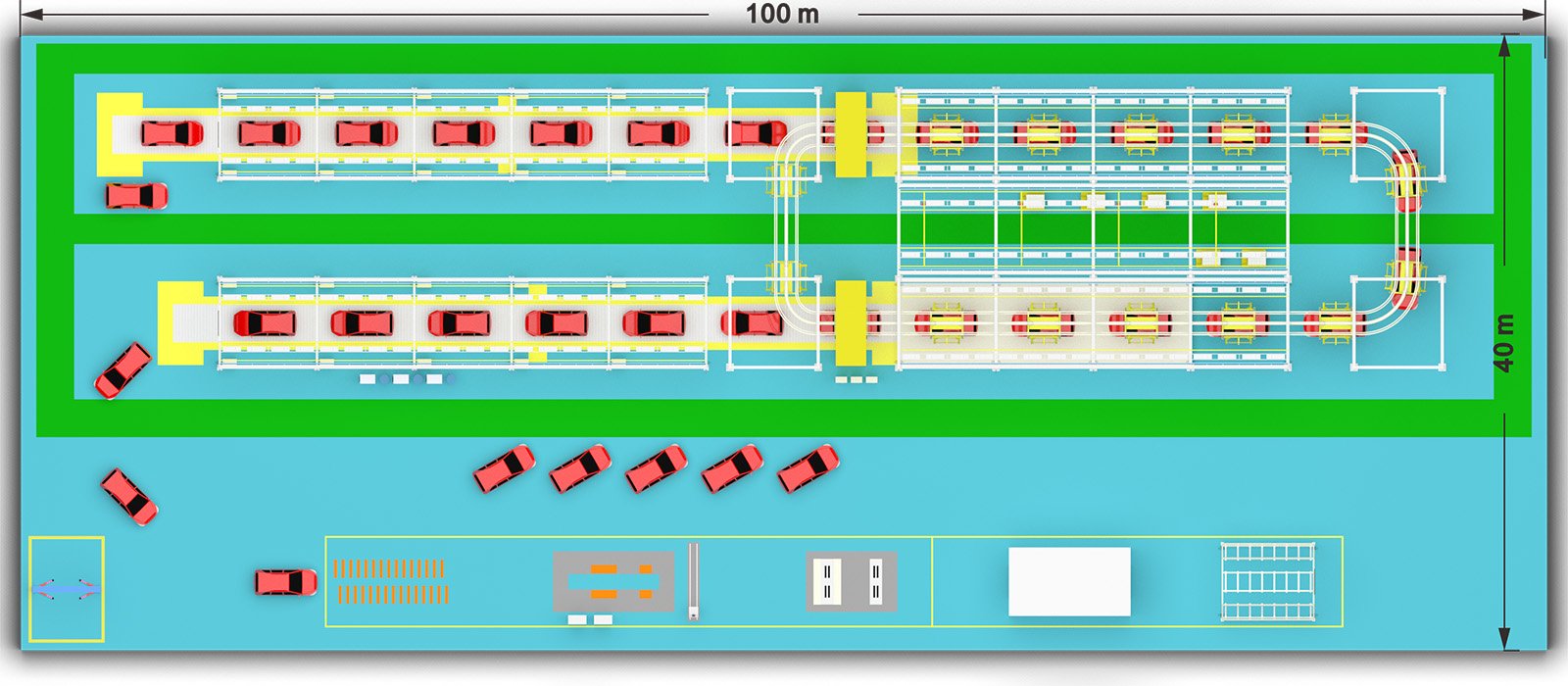
This is an SKD production assembly line designed based on a workshop size of 100 meters by 40 meters. It can meet the assembly, production, and testing requirements for fuel-powered sedans and SUVs, hybrid sedans and SUVs, and pure electric vehicles.
The production workshop is crucial to the SKD (Semi-Knocked Down) production line as it is the core area of the entire production process, directly impacting production efficiency, product quality, and cost control. Here are several key points highlighting the importance of the production workshop to the SKD production line:
- Space Planning: The spatial layout and size of the workshop must be able to accommodate all necessary production stages such as the pre-assembly line, final assembly line, inspection stations, painting shops, and storage areas to ensure smooth production processes.
- Flexibility: The workshop design needs to have a certain degree of flexibility to adapt to changes in vehicle models and production requirements, including quickly adjusting the production line to fit new vehicle models.
- Efficiency: The layout of the workshop and the configuration of the production line directly affect production efficiency. A well-planned layout can reduce material handling time and improve worker efficiency.
- Quality Control: The workshop must include quality inspection stations to ensure that the quality of products at each production stage meets standards and to identify and resolve issues promptly.
- Safety: The workshop must adhere to strict safety standards, including equipment safety, worker safety, and environmental safety, to prevent accidents and ensure employee health.
- Environmental Control: The environmental conditions within the workshop, such as temperature, humidity, dust, and noise levels, need to be properly controlled to protect worker health and product quality.
- Logistics Coordination: The workshop needs to be closely coordinated with the logistics system to ensure the timely supply of raw materials and components, as well as the smooth transportation of finished products.
- Technical Support: The workshop should be equipped with necessary technical support and maintenance teams to ensure the stable operation of the production line and to troubleshoot promptly.
- Cost Control: The operating costs of the workshop directly affect the cost-effectiveness of the entire SKD production line. Effective space utilization and resource management help to reduce costs.
- Sustainability: Modern production workshops should also consider environmental impact and energy efficiency, adopting energy-saving technologies and materials to achieve sustainable development.
In summary, the production workshop is the foundation for the successful operation of the SKD production line, and it needs to consider a variety of factors to ensure that the production process is efficient, safe, and economical.
Regarding the SKD production line’s capacity
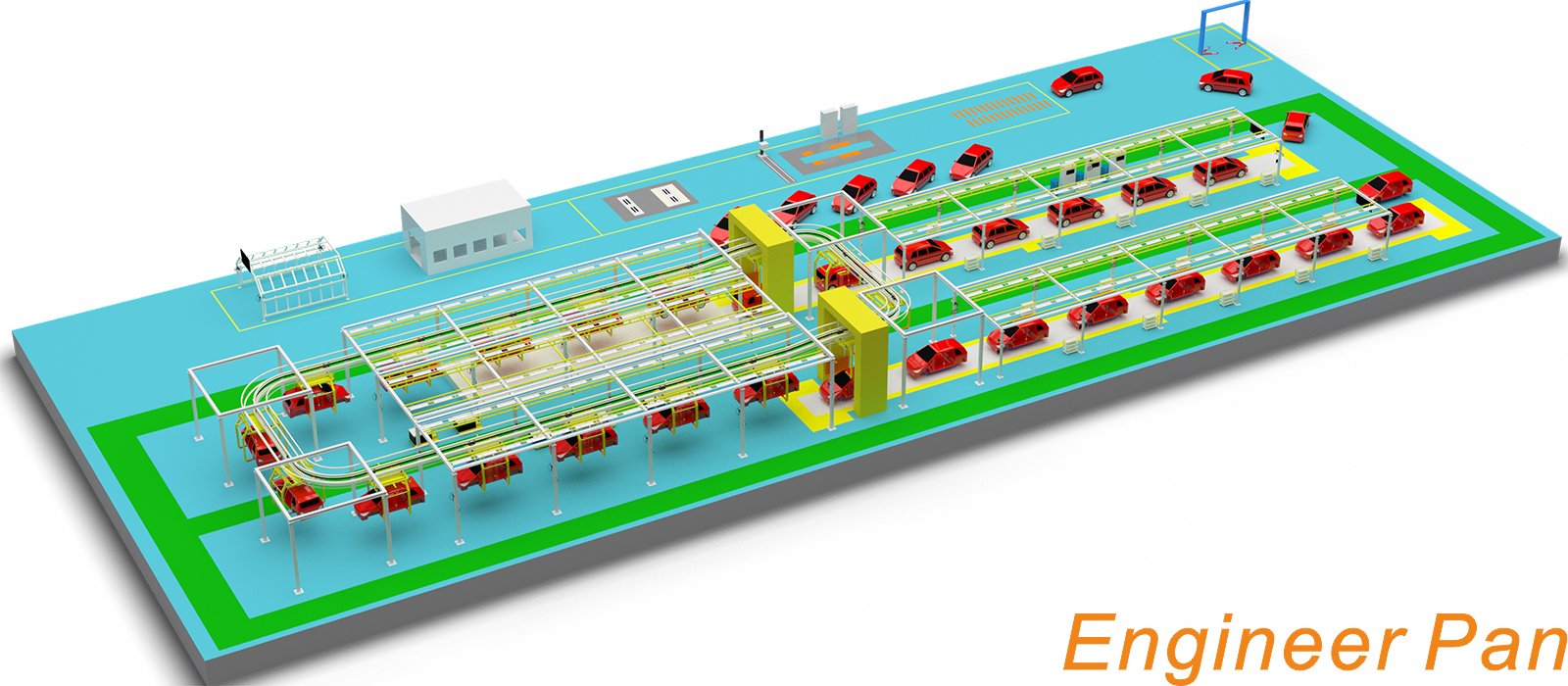
The designed production capacity of this SKD production line is 3 to 5 JPH
JPH (Jobs Per Hour) is a key metric for measuring the production efficiency in the automotive manufacturing industry, representing the workload per hour and used to reflect the theoretical production capacity of a production line or an entire factory. It plays a crucial role in factory planning, equipment selection, process layout, and matching production capabilities, helping companies optimize their production processes, ensure smooth and efficient operation of the production lines, and prevent bottlenecks and resource waste.
What functions can this SKD production line achieve
The SKD production line for sedans and SUVs consists of the following equipment, which can achieve the corresponding functions:
- Pre-assembly workstation:
- Function: Assemble the main components of the vehicle, such as the engine, transmission, suspension system, and axles.
- Body assembly line:
- Function: Assemble the vehicle body structure, including body panels, doors, roof, and interior components.
- Assembly line:
- Function: Assemble the vehicle’s interior, seats, dashboard, electronic devices, etc.
- Inspection station:
- Function: Inspect the assembled vehicle to ensure all parts are correctly installed and meet performance standards.
- Tire and wheel assembly equipment:
- Function: Install tires and wheels, ensuring proper balance and alignment.
- Engine and powertrain test bench:
- Function: Test the performance of the engine and powertrain to ensure they operate correctly.
- Final inspection line:
- Function: Conduct a comprehensive vehicle inspection, including lighting, brakes, emissions, etc.
- Quality control station:
- Function: Perform the final quality check to ensure the vehicle meets the factory standards.
- Logistics system:
- Function: Coordinate the supply of raw materials and components, as well as the storage and transportation of finished vehicles.
- Information management system:
- Function: Track production progress, manage inventory, and record quality control data.
- Automated material handling system (such as AGVs – Automated Guided Vehicles):
- Function: Automate the transportation of raw materials and semi-finished goods, reducing manual handling.
These pieces of equipment and functions together form a complete SKD production line, capable of efficiently assembling sedans and SUVs while ensuring product quality and production safety.
Customization of the SKD production line
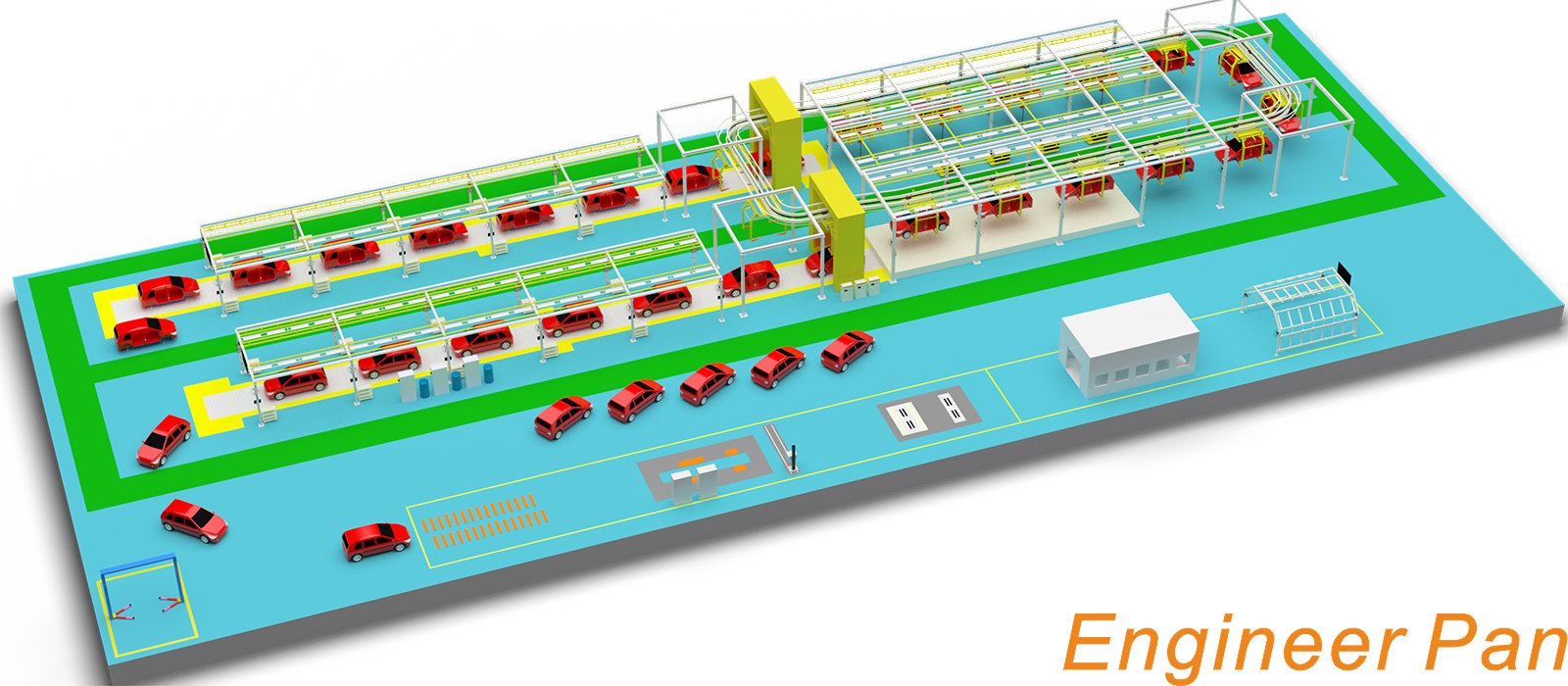
Customization of an SKD production line is a tailored approach that takes into account the specific vehicle types to be produced by the customer, the dimensions of the production workshop, the required production capacity, and the desired level of automation. This process ensures that the SKD line meets the unique needs and constraints of the manufacturer, optimizing production efficiency, quality, and cost-effectiveness while accommodating the assembly of sedans, SUVs, or other vehicle models within the given space and output targets.