An anti-static, constant temperature, constant humidity, and dust-free cleanroom is a specialized production environment designed to meet strict requirements in industries like electronics, pharmaceuticals, and precision manufacturing. It features anti-static materials, precise temperature and humidity control, and high-efficiency air filtration systems to maintain a dust-free environment. The cleanroom is equipped with positive pressure to prevent contamination and uses advanced airflow organization to ensure uniform air distribution. Regular maintenance, including cleaning, disinfection, and equipment calibration, ensures its optimal performance. This controlled environment is crucial for high-precision production, ensuring product quality and consistency.
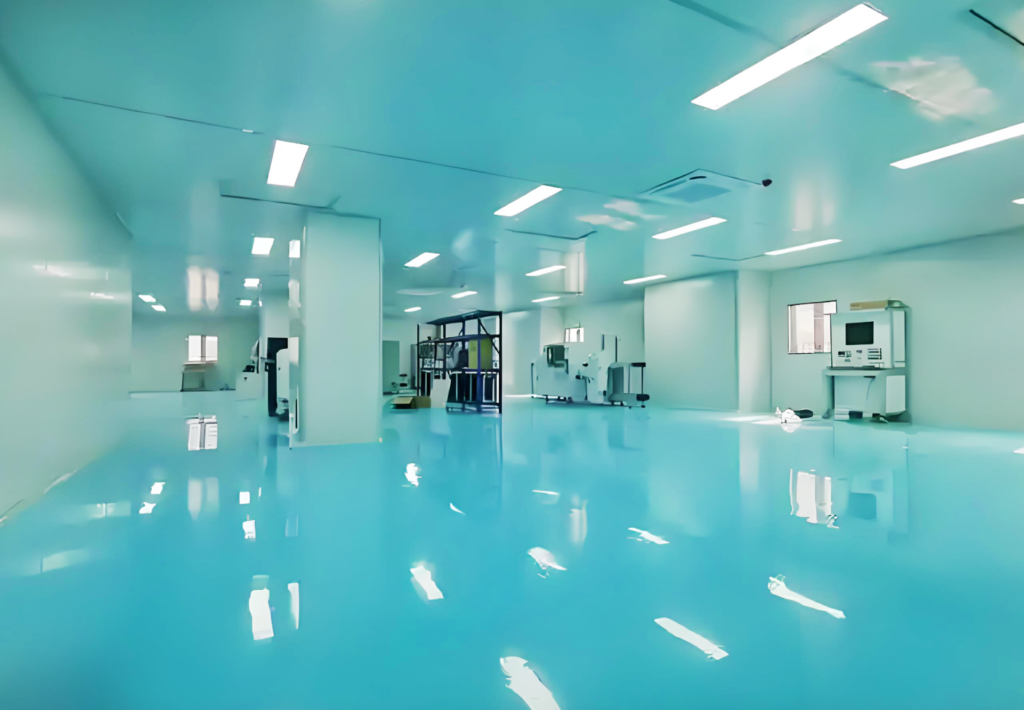
An anti-static, constant temperature, constant humidity, and dust-free cleanroom is a highly specialized and precision production environment widely used in industries with extremely strict environmental requirements. Below is a detailed introduction:
I. Functions and Features
- Anti-static Function
- Material Selection: The floors and workbenches in the cleanroom are typically made of anti-static PVC flooring or epoxy self-leveling materials, which have good electrical conductivity to effectively prevent the accumulation of static electricity.
- Environmental Control: Increasing the relative humidity (usually controlled between 35% and 40%) helps reduce the generation of static electricity.
- Grounding Measures: Equipment, personnel, and materials are all grounded to ensure that static electricity can be promptly conducted away.
- Constant Temperature and Humidity Control
- Temperature Control: Through a precision air conditioning system, the temperature inside the cleanroom is strictly controlled at 22°C ± 2°C.
- Humidity Control: The relative humidity is usually maintained between 45% and 55% to ensure the stability of the production environment.
- Stability: The temperature and humidity control system can effectively reduce fluctuations caused by changes in external climate and production activities.
- Dust-free Environment
- High-efficiency Air Filtration: High-efficiency particulate air (HEPA) filters and ultra-low penetration air (ULPA) filters are used to remove particles, microorganisms, and other contaminants from the air.
- Airflow Organization: Depending on the cleanroom class, vertical or horizontal laminar airflow is selected to ensure that air flows at a uniform speed, avoiding turbulence and dead zones.
- Positive Pressure Environment: The cleanroom is kept at a positive pressure to prevent the ingress of external contaminants.
II. Application Fields
- Electronics Industry
- Semiconductor Manufacturing: In the chip manufacturing process, key steps such as photolithography, etching, and thin-film deposition need to be carried out in a cleanroom environment to prevent the impact of particles and static electricity on electronic components.
- Integrated Circuit Packaging: Ensuring the high purity of the packaging process reduces product defects caused by external contamination.
- Biopharmaceutical Industry
- Pharmaceutical Production: A cleanroom can effectively prevent microbial contamination, ensuring the quality and safety of pharmaceuticals.
- Biologics Manufacturing: The production of vaccines, antibody drugs, and other biologics requires a sterile environment.
- Precision Instrument Manufacturing
- Optical Instruments: The production of high-precision optical lenses, telescopes, and other products tolerates no dust. A cleanroom provides an ideal processing environment.
- Aerospace Components: With extremely high cleanliness requirements, a cleanroom reduces the impact of tiny particles on products.
- Food Processing Industry
- High-quality Food Production: For products such as dairy products, baked goods, and pharmaceutical-grade health supplements, a cleanroom reduces the risk of cross-contamination by controlling airborne particles, microorganisms, and harmful gases.
- New Energy Industry
- Solar Panels and Lithium Battery Manufacturing: A dust-free environment is required to ensure product quality and consistency.
III. Design and Construction
- Layout Planning
- Flow Path Planning: The movement paths of personnel and materials are rationally planned to avoid cross-contamination.
- Buffer Zone Setup: Buffer zones should be set up around the cleanroom to reduce the impact of external contamination on the production environment.
- Air Purification System
- Filter Selection: Depending on the cleanroom class, primary, secondary, and high-efficiency filters are selected.
- Airflow Pattern: Laminar airflow (vertical or horizontal) is used to ensure that air flows at a stable speed through the working area.
- Construction Materials
- Walls and Floors: Walls are often made of sandwich panels, while floors are made of epoxy self-leveling or PVC flooring. These materials are not only anti-static and corrosion-resistant but also easy to clean and maintain.
- Sealing: All gaps are sealed with sealant to ensure the airtightness of the cleanroom.
- Pressure Differential Control
- Positive Pressure Environment: By controlling the air pressure inside the cleanroom to be higher than the external pressure, the ingress of external contaminants is prevented.
IV. Maintenance and Management
- Regular Testing
- Environmental Monitoring: Professional particle counters, microbial samplers, and other devices are used to regularly test indicators such as the number of airborne particles and microorganisms in the cleanroom.
- Equipment Calibration: Regular calibration of temperature and humidity sensors, filters, and other equipment ensures their normal operation.
- Cleaning and Disinfection
- Cleaning Requirements: Cleaning is performed using lint-free cloths, special cleaning agents, and vacuum cleaners for HEPA filters.
- Disinfection Measures: Regular disinfection of the cleanroom prevents microbial growth.
- Personnel and Material Management
- Personnel Purification: Before entering the cleanroom, personnel must pass through an air shower to remove dust particles from their clothing.
- Material Purification: Materials are transferred into the cleanroom through pass-through windows or airlocks to prevent the ingress of contaminants.
Anti-static, constant temperature, constant humidity, and dust-free cleanrooms provide an ideal environment for high-precision production by comprehensively controlling static electricity, temperature, humidity, and cleanliness. They are widely used in high-tech industries.