Assembly line with plate chain conveyor
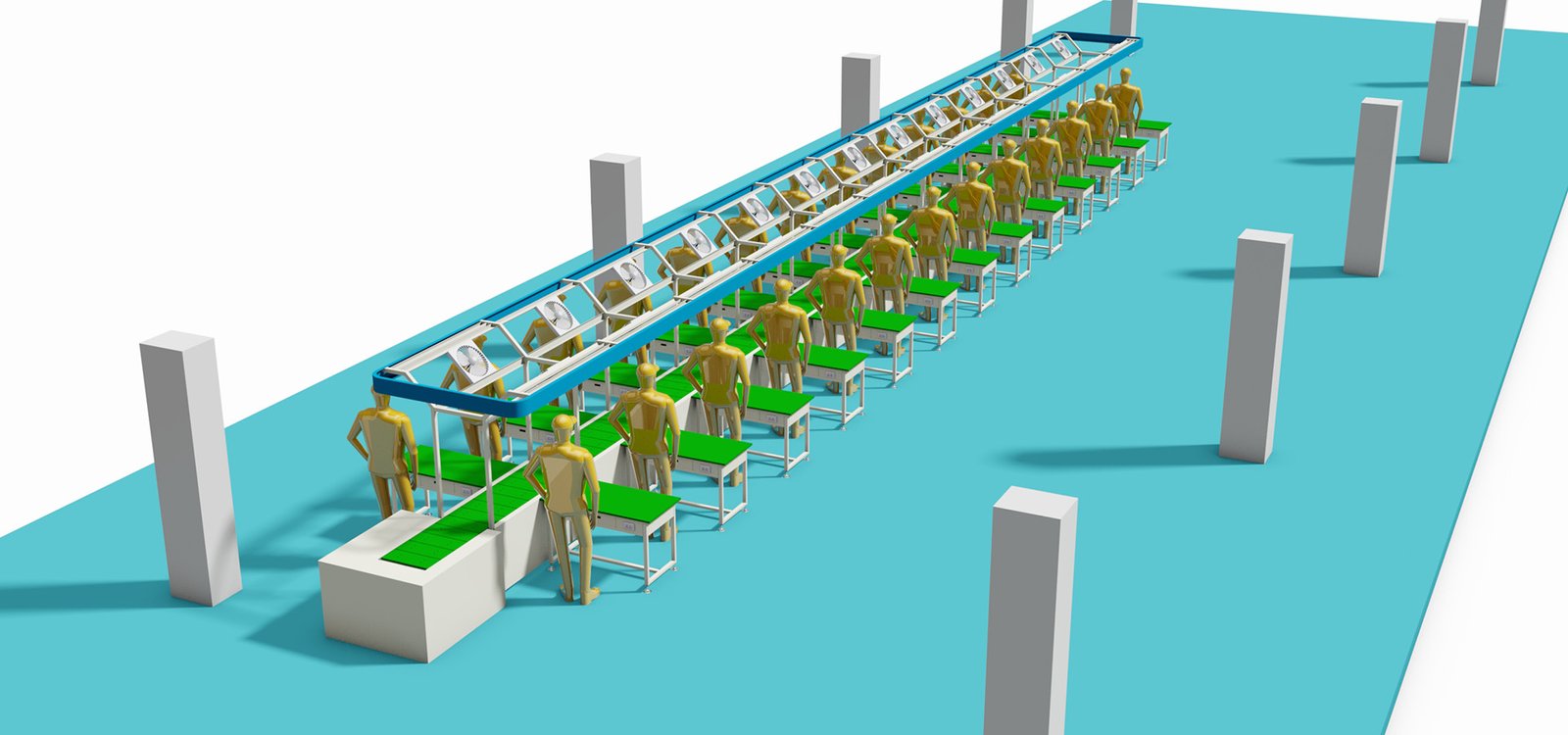
Plate chain conveyors have a variety of applications in industrial production, and they are commonly used in the following areas:
- Heavy Material Handling: Plate chain conveyors can withstand heavy loads and are suitable for long-distance transportation of heavy materials, such as in the assembly and conveying of automobiles, motorcycles, home appliances (televisions, washing machines, refrigerators, etc.), large electrical appliances, and electromechanical industries.
- Food and Beverage Industry: Because plate chain conveyors can be washed directly with water or soaked in water, they are widely used in the food and beverage industry, especially in environments that require cleanliness and hygiene.
- Electronics and Electrical Assembly: In the field of electronics and electrical assembly, plate chain conveyors are used to support delicate assembly work, ensuring the smooth movement of components along the production line.
- Automotive Manufacturing: In the automotive manufacturing process, plate chain conveyors are used in interior assembly lines, exterior trim adjustment lines, final assembly lines, and inspection lines, effectively improving the level of automation in car production.
- Chemical and Building Materials Industry: Plate chain conveyors are also widely used in the chemical and building materials industries for the transportation of cement, plastic pellets, alumina, and other solid granular materials.
- Flexibility and Adaptability: The design of plate chain conveyors allows them to complete horizontal, inclined, and turning conveyance on a single conveyor line, providing high layout flexibility.
- Maintenance and Cleaning: The mechanical part of plate chain conveyors is simple, runs smoothly, and is easy to maintain and clean, which is essential for keeping production lines hygienic and reducing downtime.
- Durability and Reliability: The plates and chains of plate chain conveyors are usually made of high-strength alloy steel, ensuring the strength and durability of the conveying system, suitable for high-volume, long-distance material transportation needs.
- Energy Efficiency: Plate chain conveyors rely on the internal friction of the material for transportation, with low energy consumption, about 40% less power consumption than traditional screw conveyors.
- Low Cost and High Efficiency: Plate chain conveyors are convenient to install and maintain, with a simple structure, high transmission speed, and stability, making them suitable for low-cost, high-efficiency production requirements.
In summary, plate chain conveyors play an important role in a variety of industrial production environments due to their durability, adaptability, and ease of maintenance.
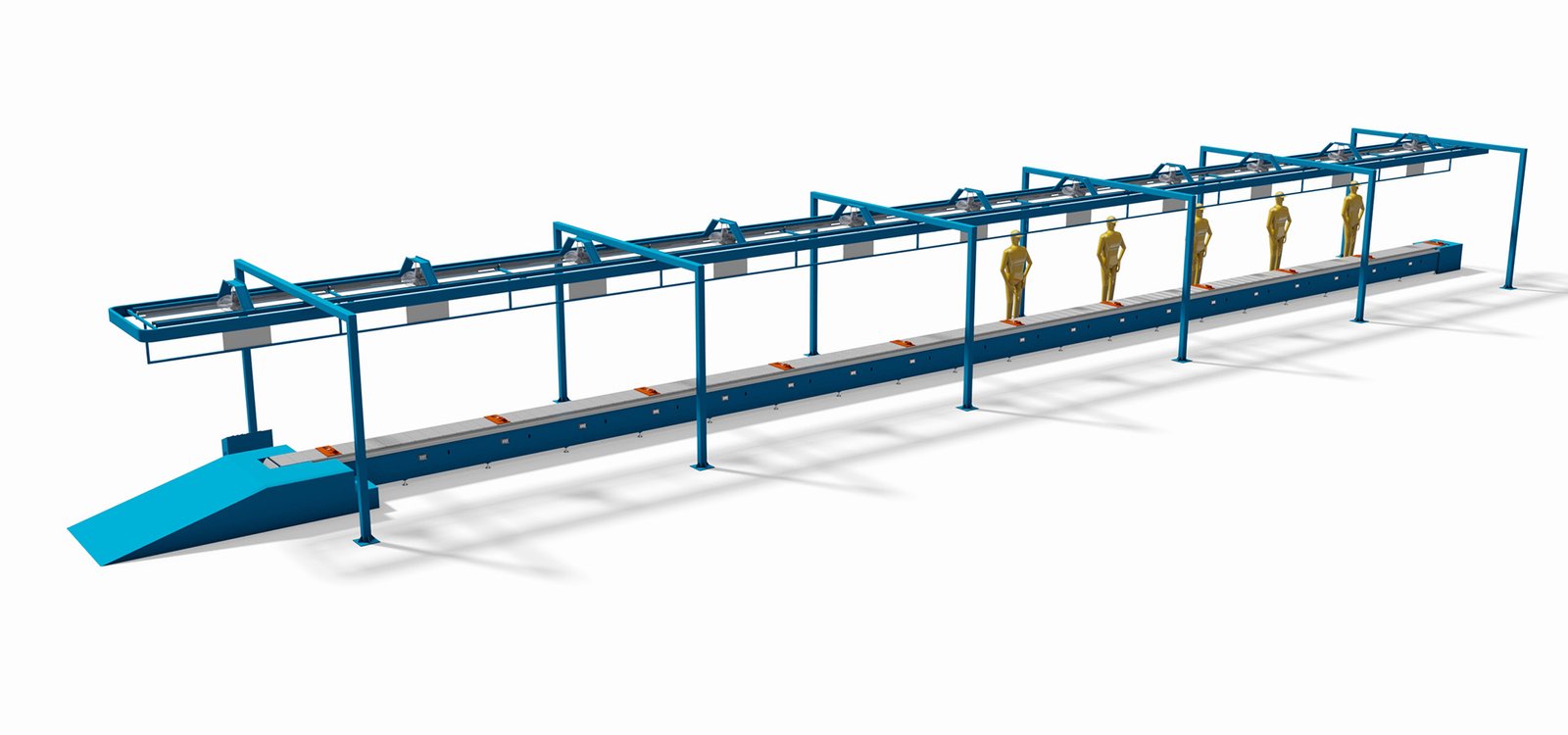
Plate chain conveyors, when used as assembly lines, have the following characteristics:
- High Load Capacity: Plate chain conveyors can handle heavy loads, making them suitable for heavy-duty assembly tasks.
- High Stability: The plate chain structure is stable and can maintain precise synchronization at high speeds, ensuring a smooth assembly process.
- Wide Adaptability: They can be designed in straight lines, curves, or combinations to fit complex factory layouts and assembly requirements.
- Easy Maintenance: The components of plate chain conveyors are easy to disassemble and replace, facilitating routine maintenance and troubleshooting.
- Flexibility: The chain speed can be adjusted to accommodate different production rhythms and assembly needs.
- Durability: Plate chain conveyors are typically made of durable materials such as carbon steel or stainless steel, allowing for long-term use in harsh industrial environments.
- Safety: The design of plate chain conveyors can include safety devices like emergency stop buttons and protective barriers to protect the safety of operators.
- Modular Design: The modular design of plate chain conveyors allows for easy expansion or reconfiguration to adapt to production changes.
- Automation Integration: They can be integrated with automated equipment such as robots and automatic assembly machines to achieve automated assembly processes.
- Ease of Cleaning: Especially for the food and pharmaceutical industries, plate chain conveyors can be designed to be easily cleaned and meet hygiene standards.
- Reduction of Manual Labor: Plate chain conveyors can reduce manual handling and operations, lowering physical labor intensity and increasing work efficiency.
- Adjustability: The height and incline angle of plate chain conveyors can be adjusted as needed to accommodate different assembly tasks.
- Energy Efficiency: Compared to other types of conveying systems, plate chain conveyors can be more energy-efficient.
- Suitable for Various Environments: Plate chain conveyors can be used in a variety of environments, including high-temperature, low-temperature, high-humidity, and dusty conditions.
These characteristics make plate chain conveyors an ideal choice for many heavy industries and manufacturing assembly lines, especially in situations that require high load capacity and stability.
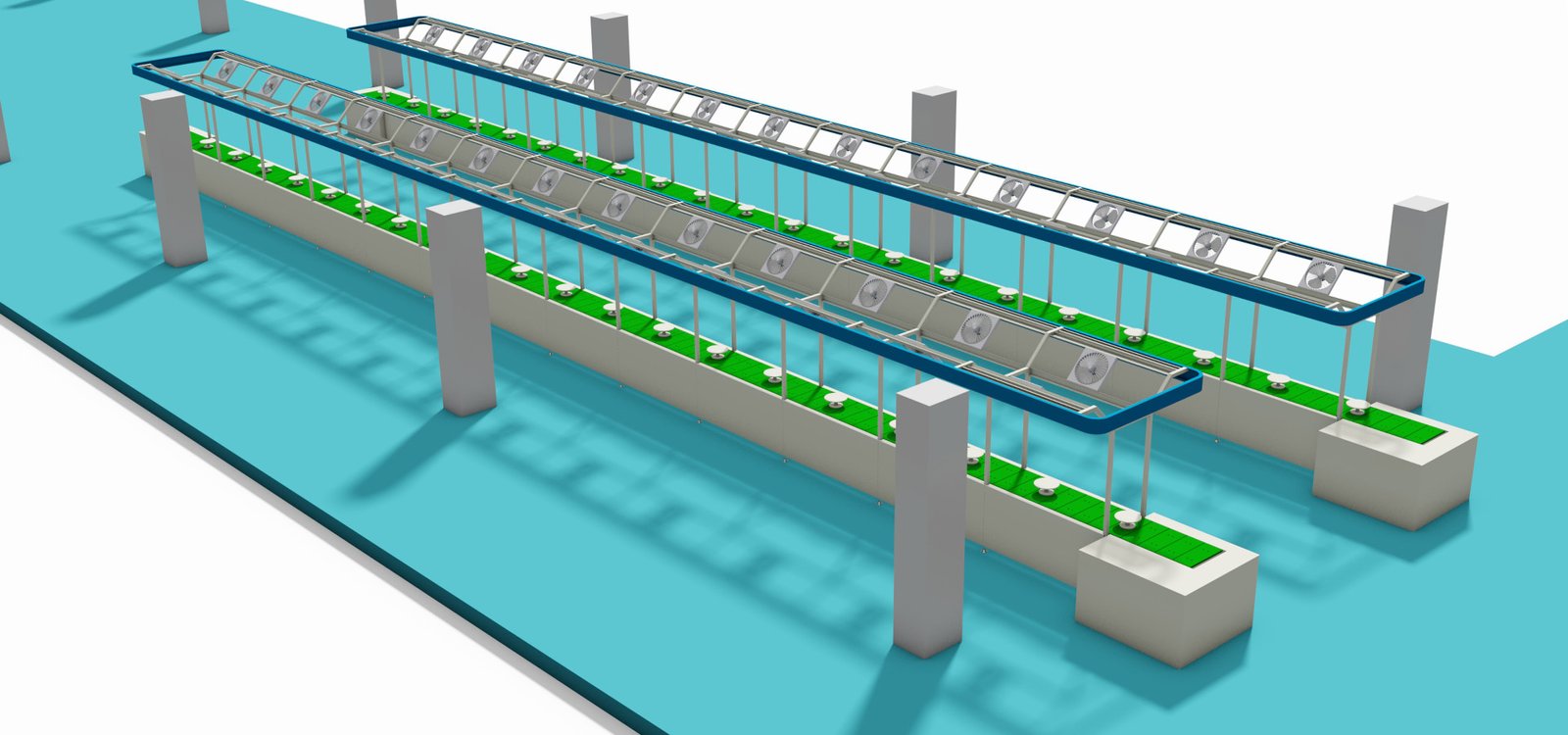
When customizing a plate chain conveyor, several factors need to be considered to ensure it meets specific production requirements and environmental conditions. Here are some key factors:
- Load Capacity: Determine the maximum weight the conveyor needs to support to select the appropriate plate chain and chains.
- Size and Shape: Design the conveyor according to the product size and shape, including the width, length, and spacing of the plate chains.
- Conveying Speed: Determine the speed of the conveyor based on production efficiency requirements and whether variable speed control is needed.
- Working Environment: Consider the environment in which the conveyor will operate, such as temperature, humidity, cleanliness requirements, and the presence of corrosive or flammable substances.
- Material Selection: Choose the right materials, such as carbon steel, stainless steel, or plastic, to meet wear resistance, corrosion resistance, and hygiene requirements.
- Turning and Inclining: If the conveyor needs to turn or incline, design the appropriate turning radius and incline angle.
- Drive System: Select the appropriate drive system, including motors, reducers, and sprockets, to ensure stable power transmission.
- Safety Features: Include emergency stop buttons, protective barriers, and other safety devices to ensure the safety of operating personnel.
- Maintenance and Cleaning: Consider the maintenance and cleaning requirements of the conveyor, ensuring it is designed for easy routine maintenance and cleaning.
- Scalability: Consider future expansion needs to ensure the conveyor design allows for future upgrades and extensions.
- Cost-Effectiveness: Evaluate the cost-effectiveness of different design schemes, choosing a solution that meets the requirements while being the most cost-effective.
- Compatibility: Ensure the conveyor is compatible with other production equipment and systems, such as automated workstations, robots, and other conveyor systems.
- Control System: Consider the level of control required, including basic start/stop control or more complex programming logic and sensor integration.
- Noise Level: Assess and control the noise generated during the operation of the conveyor to meet the noise standards of the working environment.
- Energy Efficiency: Consider the energy efficiency of the conveyor, choosing a design with high energy efficiency to reduce long-term operating costs.
- Regulatory Compliance: Ensure the conveyor design complies with local industrial safety and health regulations.
By considering these factors comprehensively, a plate chain conveyor can be customized that meets production needs, budget, and safety standards.