A CNC lathe with material storage and a gantry robot is a highly integrated automated machining device that combines the high-precision machining capabilities of a CNC lathe, an automated loading and unloading system, and material storage functions. It is widely used in the manufacturing of automotive parts, mechanical machining, and electronic device production. Below is a detailed description of the equipment, including its main components, functional features, technical parameters, and application scenarios.
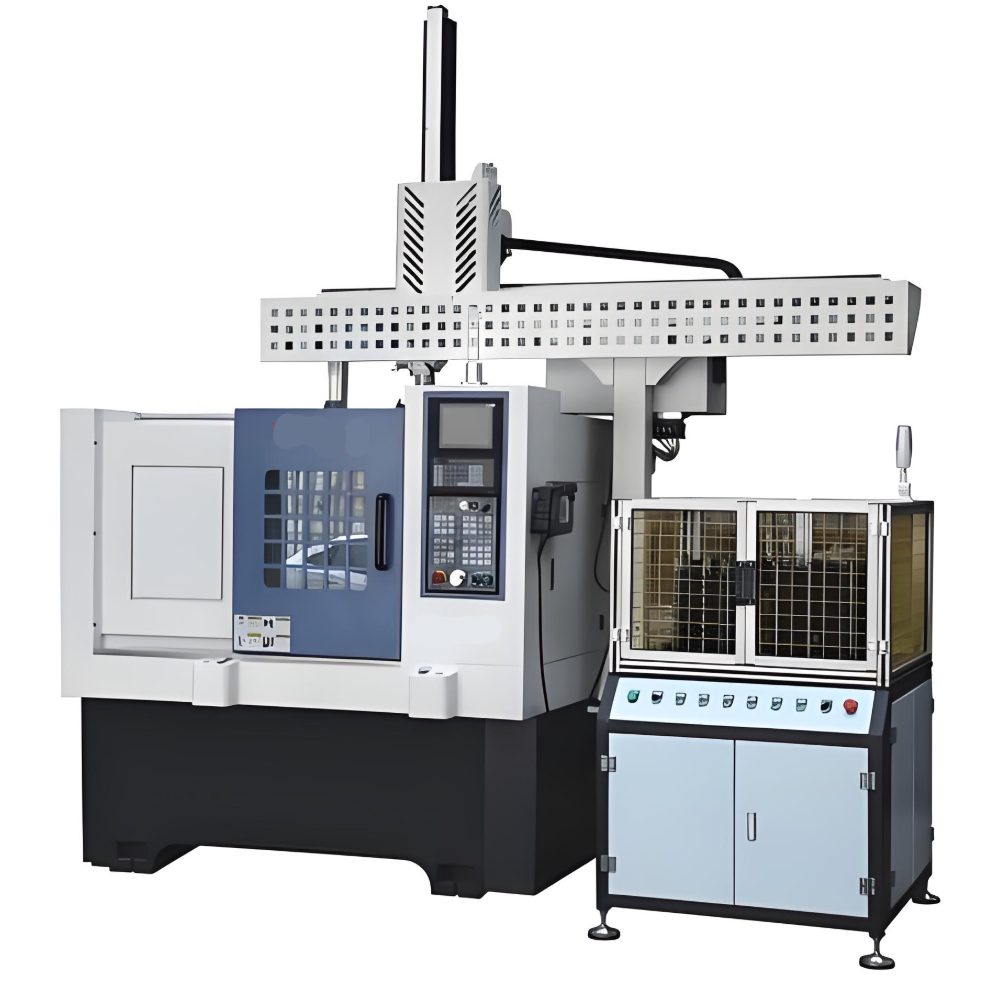
I. Components of the Equipment
- CNC Lathe Main Body
- Bed and Guide Rails:
- Made from high-strength cast iron, the bed is precision-machined and heat-treated to ensure the machine’s high rigidity and stability. The guide rails use high-precision linear rails to reduce friction and enhance machining accuracy.
- Spindle System:
- Equipped with a high-precision spindle capable of withstanding high speeds and torques, suitable for various machining requirements.
- Tool Turret or Tool Magazine:
- Depending on machining needs, a multi-station tool turret or tool magazine can be selected to quickly switch between various tools, meeting the needs for turning, milling, drilling, and other machining processes.
- Control System:
- An advanced CNC system is used, supporting multiple programming languages. The user-friendly interface is easy to operate. The system also features powerful fault diagnosis and alarm functions to ensure the reliability of the equipment.
- Material Storage System
- Storage Structure:
- The material storage typically adopts a multi-layer shelving structure, which can be customized according to the size and shape of the workpieces. The storage capacity can be adjusted according to production needs and generally can hold dozens or even hundreds of workpieces.
- Workpiece Storage Method:
- Workpieces are stored on pallets or racks to ensure stability within the storage area and prevent collisions or deformation. Sensors are installed inside the storage to monitor the quantity and position of the workpieces in real-time.
- Storage Management:
- The storage and retrieval of workpieces are managed through the CNC system or an independent storage management system, improving production efficiency.
- Gantry Robot
- Robot Structure:
- The gantry robot consists of a robotic arm, end-effector, and drive system. The robotic arm is made from high-strength aluminum alloy, designed for rigidity and lightweight.
- End-Effector:
- Depending on the shape and size of the workpieces, appropriate end-effectors such as pneumatic grippers or vacuum suction cups are equipped to ensure stable grasping and placement of the workpieces.
- Motion Control:
- The motion of the robot is controlled by the CNC system or an independent motion controller, capable of precise positioning and movement. The robot’s motion path can be programmed and adjusted according to machining needs.
- Automation Process:
- The robot automatically picks up workpieces from the storage, places them into the machine’s fixture, removes the machined workpieces after processing, and places them into the finished goods area or the next processing stage. The entire process is fully automated without manual intervention.
II. Functional Features
- High Degree of Automation
- Automatic Loading and Unloading:
- The gantry robot can automatically perform the loading and unloading of workpieces, significantly reducing human intervention and increasing production efficiency.
- Continuous Machining:
- The coordinated operation of the storage and robot allows the machine to continuously process multiple workpieces, enabling 24/7 non-stop operation, which is particularly suitable for mass production.
- Reduced Non-Machining Time:
- The automated loading and unloading system significantly shortens the time for workpiece clamping and replacement, improving the utilization rate of the machine.
- High-Precision Machining
- CNC System:
- The advanced CNC system can precisely control the machining process to ensure machining accuracy and repeat positioning accuracy.
- Spindle Precision:
- The high-precision spindle system can withstand high speeds and torques, ensuring the stability of the machining process.
- Tool Management:
- The multi-station tool turret or tool magazine can quickly switch tools, reducing tool change time and improving machining efficiency.
- Flexibility and Adaptability
- Multiple Machining Processes:
- The machine can perform various machining processes such as turning, milling, drilling, and tapping, meeting the machining needs of workpieces of different shapes and sizes.
- Quick Adjustment:
- The machine can be quickly adjusted according to different machining needs, such as changing tools or adjusting machining programs, to adapt to the machining of various workpieces.
- Customized Configuration:
- The storage capacity, robot travel, and end-effector can be customized according to customer needs to meet the requirements of different production scenarios.
- Safety and Reliability
- Safety Devices:
- The machine is equipped with multiple safety devices such as emergency stop buttons, safety doors, and light curtains to ensure the safety of operators.
- Fault Diagnosis and Alarm:
- The CNC system has powerful fault diagnosis and alarm functions that can promptly detect and handle equipment failures, reducing downtime.
- High-Reliability Design:
- The machine uses high-quality components and advanced manufacturing processes to ensure long-term stable operation.
III. Technical Parameters
Item | Parameter |
---|---|
Machine Model | [Specific Model] |
Spindle Speed | [Maximum Speed] rpm |
Spindle Torque | [Maximum Torque] N·m |
Tool Turret/Magazine | [Number of Tool Positions], supports turning, milling, drilling, and other machining processes |
Machining Range | Maximum Machining Diameter: [Diameter] mm Maximum Machining Length: [Length] mm |
Control System | [CNC System Brand and Model], supports multiple programming languages, with fault diagnosis and alarm functions |
Storage Capacity | [Maximum Number of Workpieces], customizable according to needs |
Robot Travel | X-axis: [Travel] mm Y-axis: [Travel] mm Z-axis: [Travel] mm |
End-Effector | Pneumatic gripper/Vacuum suction cup, customizable according to the shape and size of the workpieces |
Degree of Automation | Automatic loading and unloading, 24-hour non-stop operation, suitable for mass production |
Machining Accuracy | Repeat Positioning Accuracy: [Accuracy] mm Machining Accuracy: [Accuracy] mm |
Footprint | [Length] mm × [Width] mm × [Height] mm |
Power Requirements | [Voltage] V, [Power] kW |
Cooling System | High-efficiency cooling system to ensure the stability of the machining process |
Applicable Materials | Steel, aluminum alloy, plastic, and other materials |
Applicable Industries | Automotive parts manufacturing, mechanical machining, electronic device manufacturing, etc. |
IV. Application Scenarios
- Automotive Parts Manufacturing
- Engine Components:
- Machining key components such as crankshafts, connecting rods, and pistons to ensure their high precision and consistency.
- Transmission Components:
- Machining gear and shaft parts to improve production efficiency and product quality.
- Body Components:
- Machining large body components such as doors and frames to meet mass production needs.
- Mechanical Machining Industry
- Shaft Parts:
- Machining various shaft parts such as drive shafts and mandrels to improve machining efficiency and accuracy.
- Disc Parts:
- Machining various disc parts such as flywheels and gears to ensure dimensional accuracy and surface quality.
- Complex Parts:
- Machining complex-shaped parts such as molds and robotic arms to meet high-precision machining needs.
- Electronic Device Manufacturing
- Electronic Component Housings:
- Machining small precision parts such as electronic component housings and connectors to meet high-precision machining needs.
- Mechanical Components:
- Machining mechanical components in electronic devices such as motor housings and heat sinks to improve production efficiency and product quality.
- Mold Manufacturing:
- Machining high-precision molds to ensure the dimensional accuracy and surface quality of the molds.
Summary
A CNC lathe with material storage and a gantry robot is a highly automated and intelligent machining device that combines the high-precision machining capabilities of a CNC lathe, an automated loading and unloading system, and material storage functions. It can significantly improve production efficiency, reduce labor costs, and ensure the high precision and stability of the machining process. This equipment is widely used in the manufacturing of automotive parts, mechanical machining, and electronic device production, and is an essential efficient machining device in modern manufacturing.