
Electric scooter assembly lines are characterized by standardization, automation, efficiency, and quality control. They integrate various production processes, from component assembly to final testing, ensuring consistent quality and rapid production. Flexible and adaptable, these lines can quickly adjust to different models, enhancing market responsiveness. Digital management systems monitor production, further ensuring efficiency and product consistency.
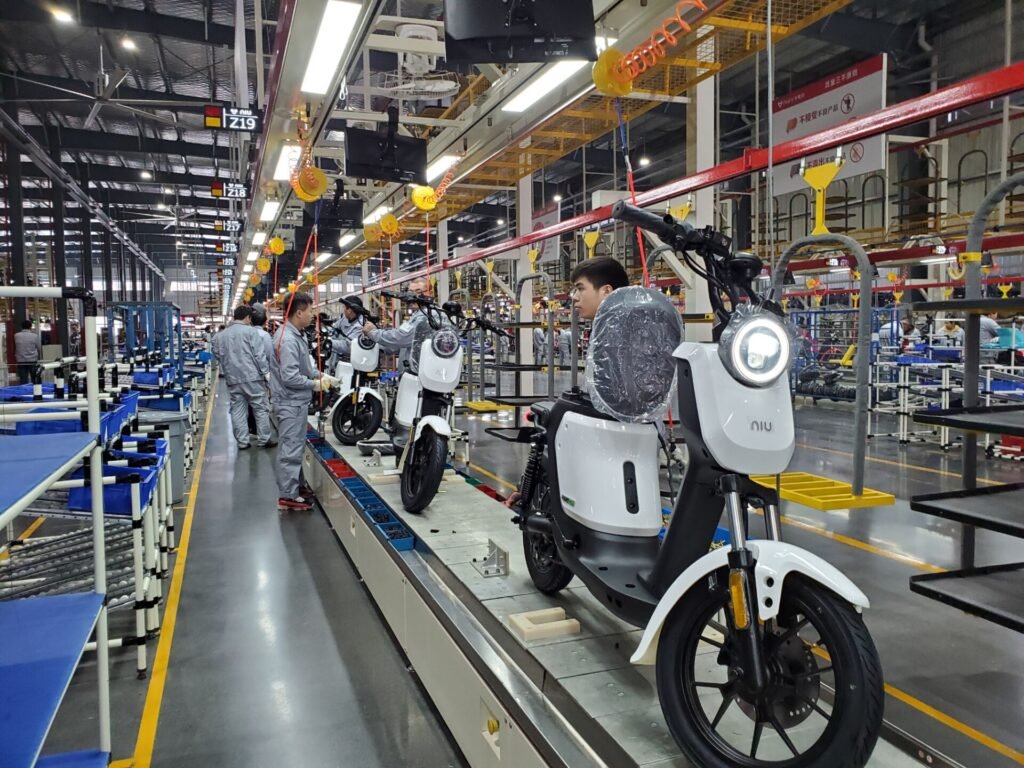

The characteristics of assembly line production for electric scooters mainly include the following aspects:
- Standardization and Modularization: The assembly process on the production line is standardized, with each workstation responsible for specific assembly tasks, such as motor installation, battery fixing, and control system assembly, ensuring consistent operation and high-quality products.
- Automation: The production line makes extensive use of automated equipment and robots, reducing manual operation and increasing production efficiency and stability.
- High Efficiency: The production line can significantly improve production efficiency and shorten the production cycle of individual products, achieving rapid assembly.
- Quality Control: The production line has multiple quality checkpoints that can detect and resolve issues in the production process in a timely manner, ensuring the performance of the entire vehicle.
- Flexibility and Adaptability: The production line is designed to be flexible and can be quickly adjusted to meet the production needs of different models, responding quickly to market changes.
- Digital Management: Real-time monitoring and management of the production process are achieved through MES systems, improving production efficiency and product quality consistency.
- Integrated Manufacturing Process: The production line integrates the entire process from raw material processing to final delivery, including frame welding, core component assembly, wheel assembly, circuit connection, exterior painting, interior assembly, functional testing, quality inspection, and more.
- Environmental Friendliness: The production process on the assembly line focuses on environmental protection, such as using pneumatic car-grade tires without inner tubes to reduce waste.
- Safety: The electric scooters assembled on the production line pay attention to safety, such as adding disc brake systems to provide better braking performance.
- Cost-effectiveness: The high efficiency and automation of the production line reduce labor costs and per-unit product costs, improving the overall economic benefits of production.
In summary, the assembly line production of electric scooters achieves high efficiency, high quality, and flexible adaptability through standardization, automation, and digital management, while focusing on environmental protection and safety, effectively enhancing the market competitiveness of the products.
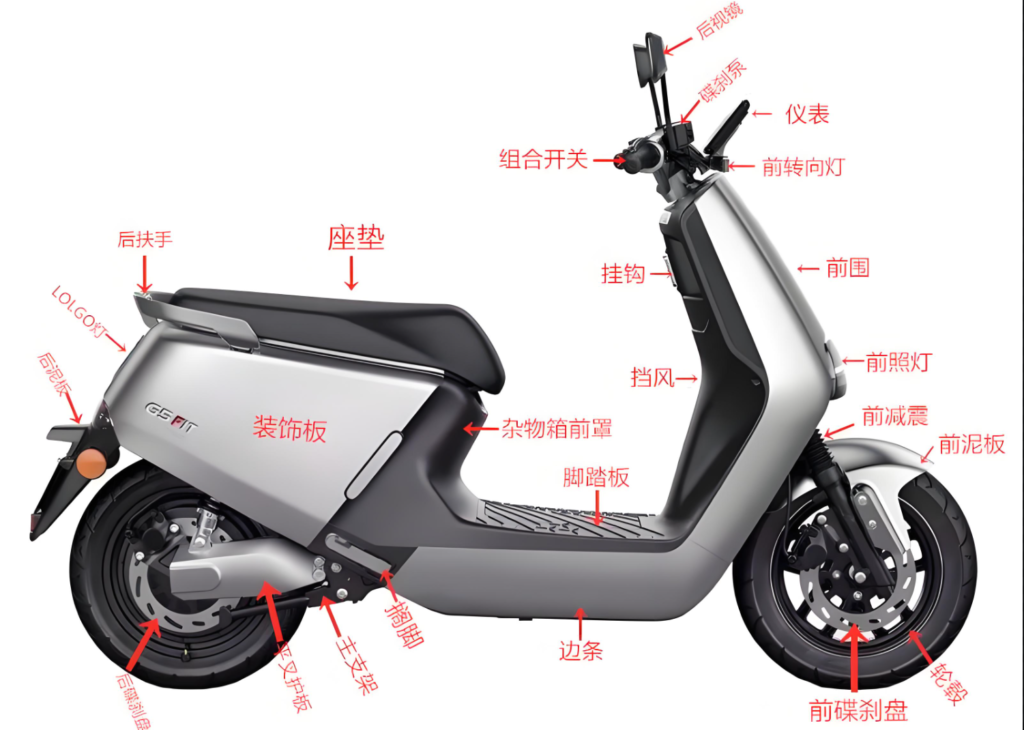
Electric scooters, also known as electric kickboards, are personal transportation vehicles powered by electricity. Their structure and features are as follows:
- Frame: Typically made of metal or alloy materials, it serves as the base structure of the entire vehicle and needs to have sufficient strength and stability.
- Battery: Provides power supply, mostly lithium battery packs, which need to have good charging and discharging performance and safety.
- Motor: Can be a hub motor or mid-mounted motor, responsible for converting electrical energy into mechanical energy to drive the scooter.
- Control System: Includes controllers and various sensors that control the working state of the motor and respond to the driver’s operations.
- Transmission System: Such as belt drive or direct drive, which transmits the power of the motor to the wheels.
- Wheels and Suspension: Including tires, hubs, etc., affecting the smoothness and passability of the vehicle’s travel.
- Braking System: Ensures the safe stopping of the vehicle, which can be electronic braking or mechanical braking.
- Other Components: Such as lights, display panels, seats, etc., providing additional functions and comfort.
Features include:
- Portability: Small in size and light in weight, making them easy to carry and store.
- Environmental Friendliness: Electric drive with no exhaust emissions, which is beneficial for environmental protection.
- Economical: Low operating costs, convenient charging, and simple maintenance.
- Easy to Operate: Easy to learn and suitable for users of all ages.
- Flexibility: Suitable for urban commuting and short-distance travel, able to flexibly navigate through congested traffic environments.
- Intelligence: Some high-end electric scooters are equipped with smart interconnectivity features, such as APP control, GPS positioning, etc.
- Safety: Usually equipped with a good braking system and lighting system to ensure safe driving at night.
- Regulatory Adaptability: Depending on the regulations of different countries and regions, the design of electric scooters will be adjusted to meet the requirements for road use.
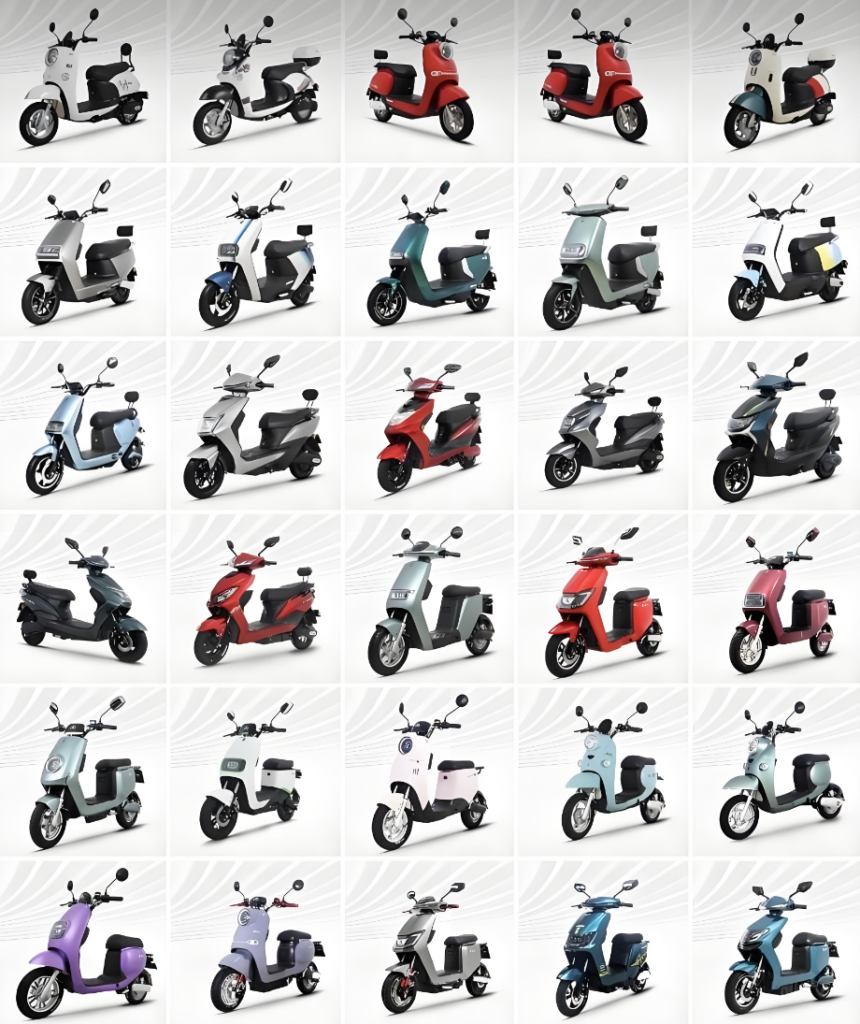
The assembly process of an electric scooter includes the following main steps:
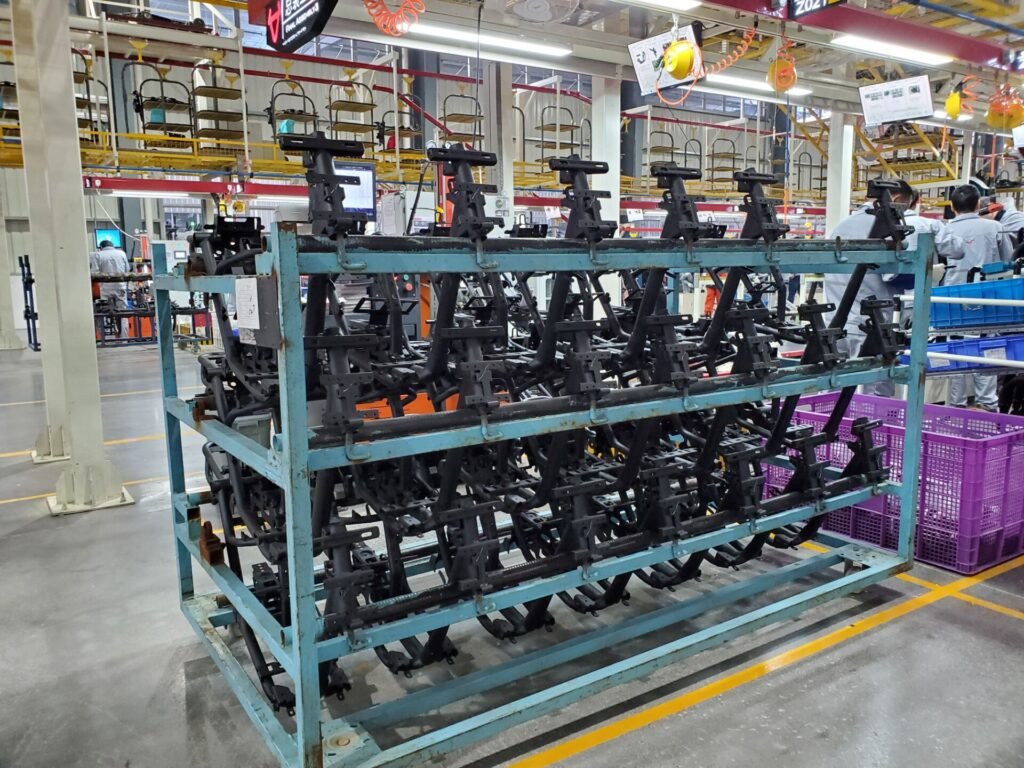
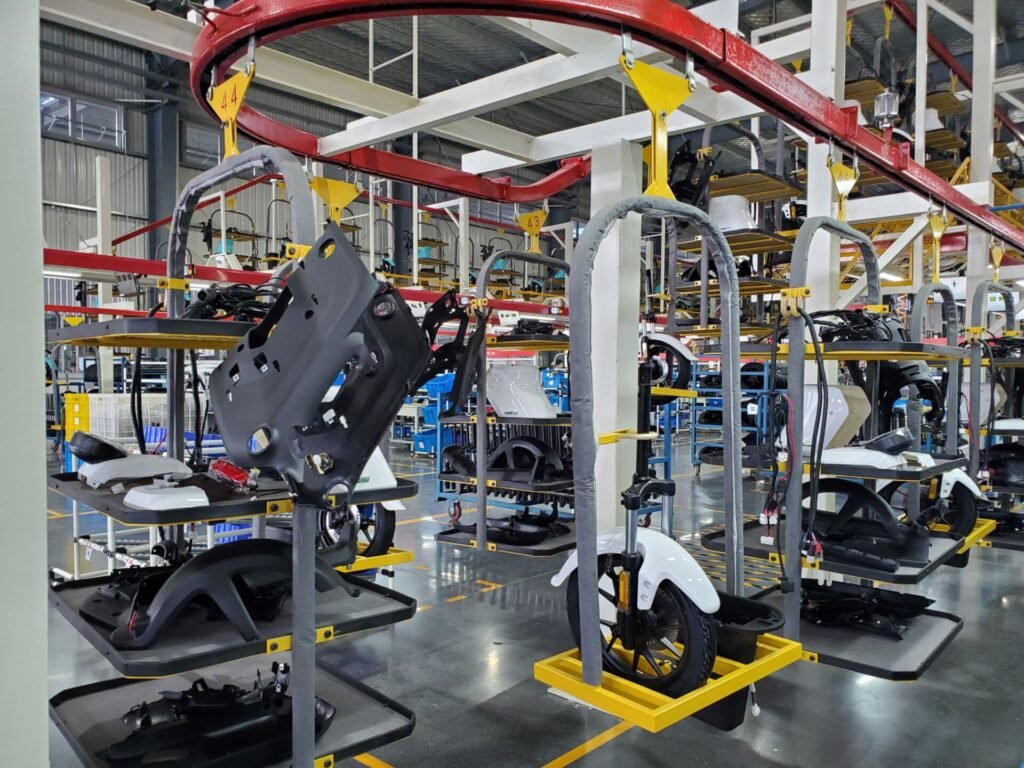
- Raw Material Preparation: This involves sorting and processing materials such as iron, aluminum, and plastic to provide qualified raw materials for subsequent processes.
- Frame Fabrication: Iron materials are processed into the frame of the electric scooter through welding and other processes, which forms the basic structure of the scooter.
- Drive System Installation: Core components such as the motor, battery, and controller are installed onto the frame; these parts are the power source of the electric scooter.
- Wheel Assembly: This includes the assembly of hubs, tires, and braking systems, and they are fixed onto the frame to ensure stable travel.
- Circuit Connection: The circuit connections between the battery and motor, and the controller and motor, are completed to ensure the normal operation of the electrical system.
- Painting: The frame is painted to enhance its appearance and provide a certain level of protection.
- Assembly and Adjustment: Accessories such as the seat, handlebars, and pedals are installed, and the motor, battery, and controller are adjusted to ensure the performance of the entire vehicle.
In terms of automated equipment, an electric scooter assembly line typically includes:
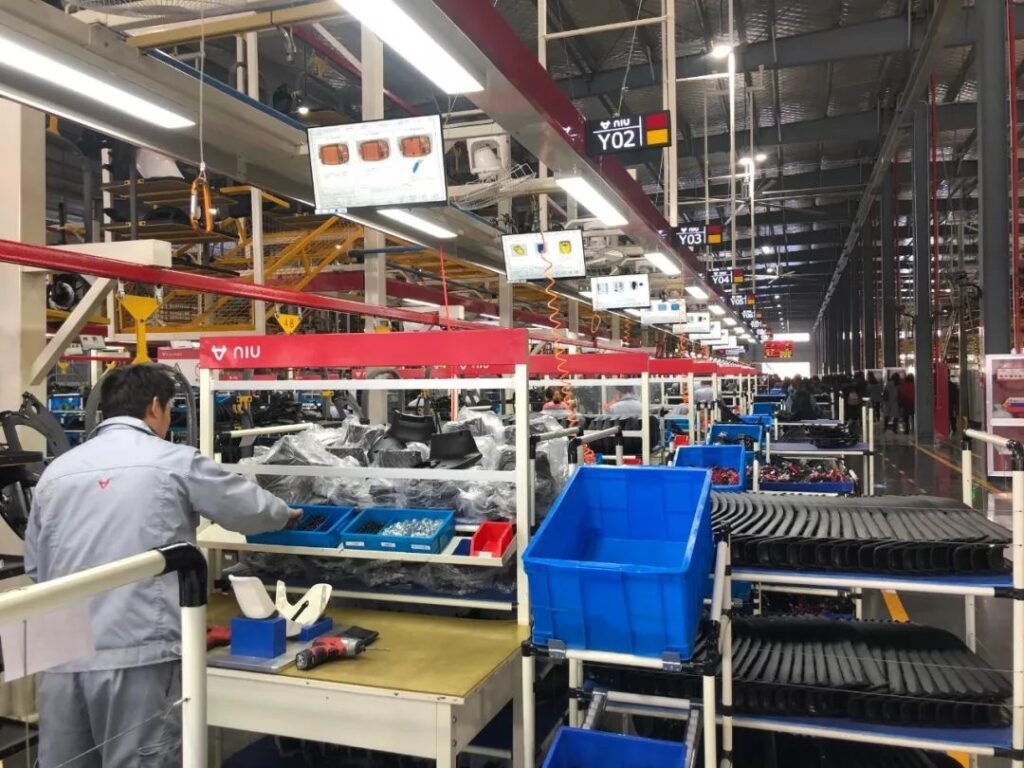
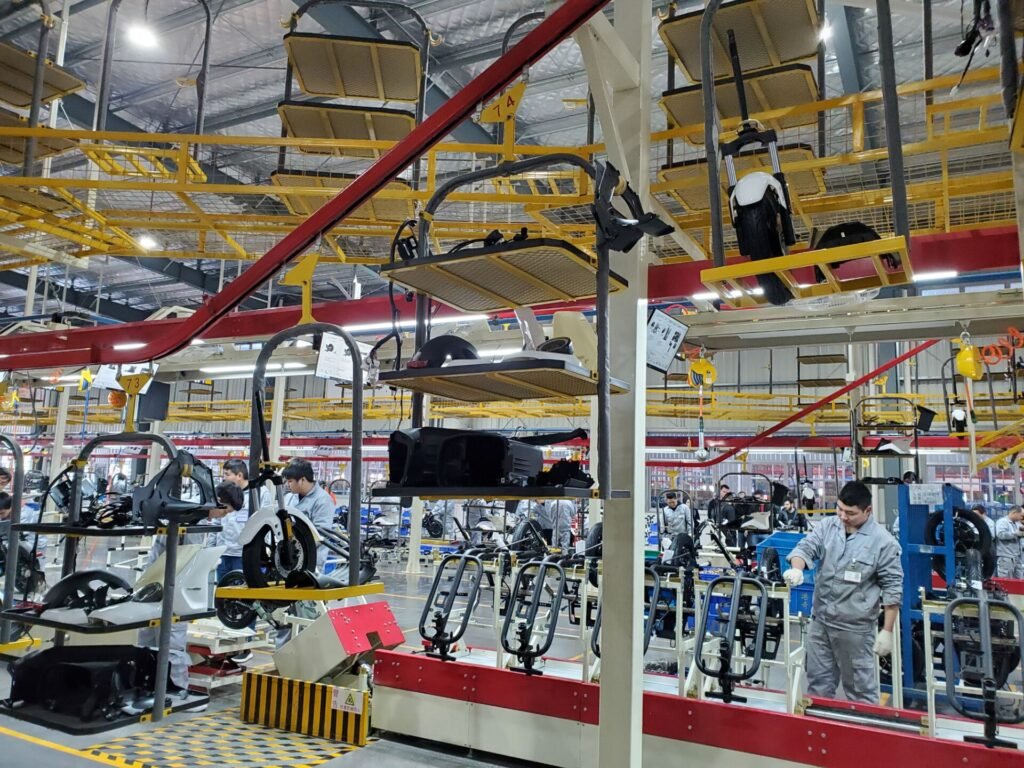
- Automated Conveyor Lines and Robots: Used for the automatic transportation of various components during the assembly process of the electric scooter.
- Battery Assembly Line: Includes processes such as assembly group technology, automatic welding, semi-finished product assembly, testing, PACK testing technology, and PACK packaging technology.
- Motor and Other Assembly Lines: Involves the manufacturing of the motor control system, mechanical reduction, and transmission devices.
- AGV (Automated Guided Vehicle) System: Used for the automated transportation of battery packs, improving production efficiency and reducing costs.
- MES (Manufacturing Execution System) Management Software: Used for the digital management of the production line, improving production efficiency and the consistency of product quality.
- Welding and Cutting Equipment: Used for processing the frame and other metal parts of the electric scooter.
- Stamping Equipment: Used for the stamping and forming of body parts for electric scooters.
- Painting Equipment: Used for the spray painting process of the electric scooter body.
- Assembly Machinery and Tools: Used for the final assembly of the electric scooter, including the assembly of batteries, motors, electronic control devices, and high-voltage wiring harnesses.
- Testing Equipment: Used for the overall testing of the vehicle, including the testing of the electric drive system and high-voltage electrical system, to enhance electrical performance and electrical safety.
The automation and informatization features of the electric scooter production line improve production efficiency and quality control levels, while reducing labor costs and per-unit product costs.
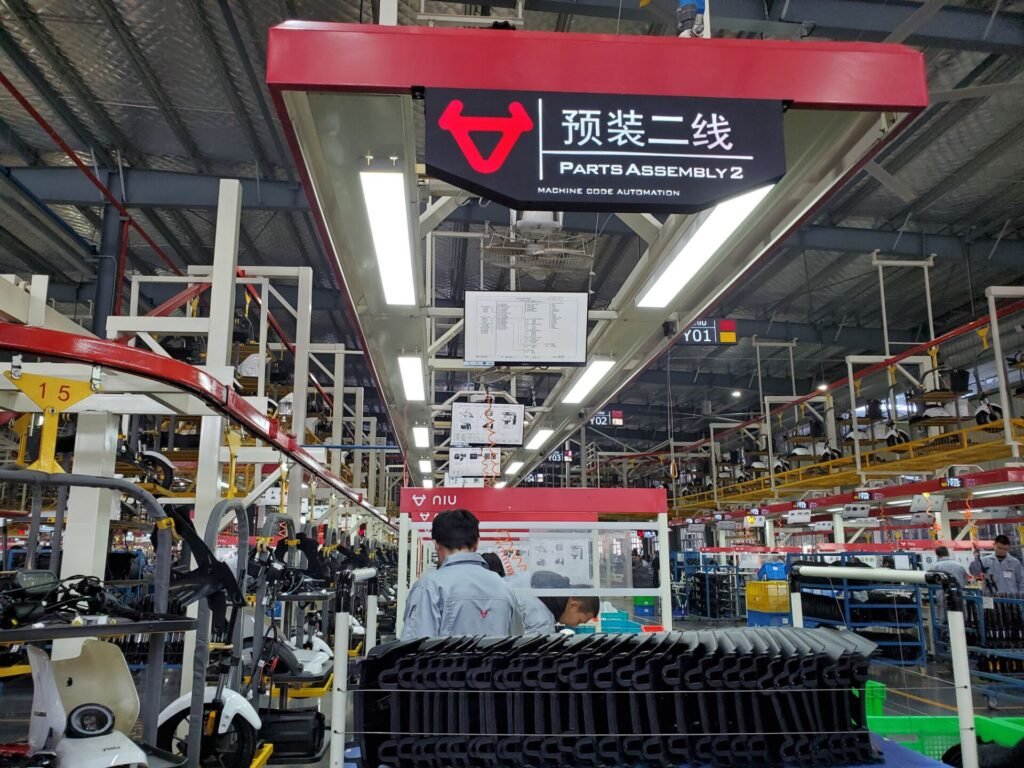
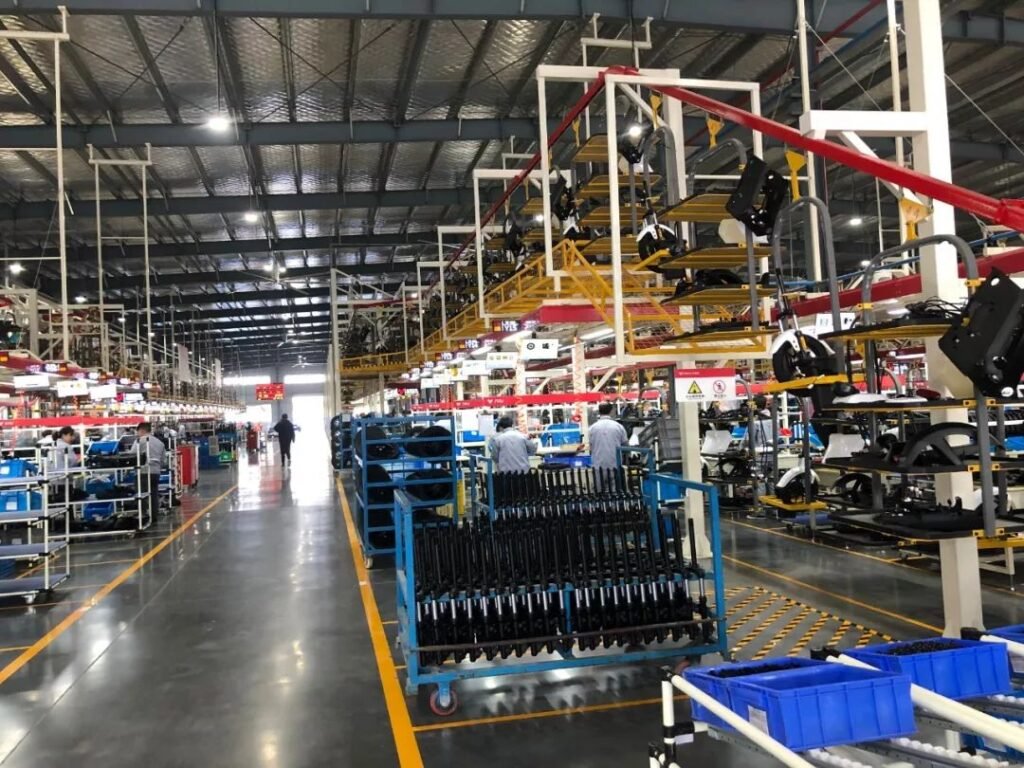
The performance testing items after the assembly of an electric scooter production line include but are not limited to:
- Electrical Performance Testing: Including battery performance, motor efficiency, and controller function testing.
- Mechanical Performance Testing: Including brake performance, suspension system, and tire wear resistance testing.
- Environmental Adaptability Testing: Simulating performance testing under different climate conditions, such as waterproof and dustproof testing.
- Safety Performance Testing: Including lighting system, signaling system, and vehicle body structure strength testing.
- Durability Testing: Assessing the durability of the vehicle through long-term cyclic testing.
- Top Speed Testing: Ensuring the vehicle can reach the claimed top speed.
- Range Testing: Evaluating the driving distance supported by the battery after a single charge.
- Electromagnetic Compatibility Testing (EMC Testing): Ensuring that the vehicle’s electronic systems do not interfere with other devices, nor are they affected by external electromagnetic interference.
The corresponding testing equipment may include:
- Battery Tester: Used to test the battery’s capacity, internal resistance, charging, and discharging performance.
- Motor Test Stand: Used to test the motor’s speed, torque, and efficiency.
- Environmental Test Chamber: Used to simulate different temperature and humidity conditions.
- Brake Tester: Used to test the performance and braking distance of the braking system.
- Fatigue Tester: Used to simulate durability testing under long-term use conditions.
- Speed Tester: Used to measure the vehicle’s top speed.
- Range Tester: Used to evaluate the battery’s endurance.
- EMC Testing Equipment: Used to test the vehicle’s electromagnetic compatibility.
These testing items and equipment ensure that the electric scooter meets safety and performance standards before being delivered to consumers.
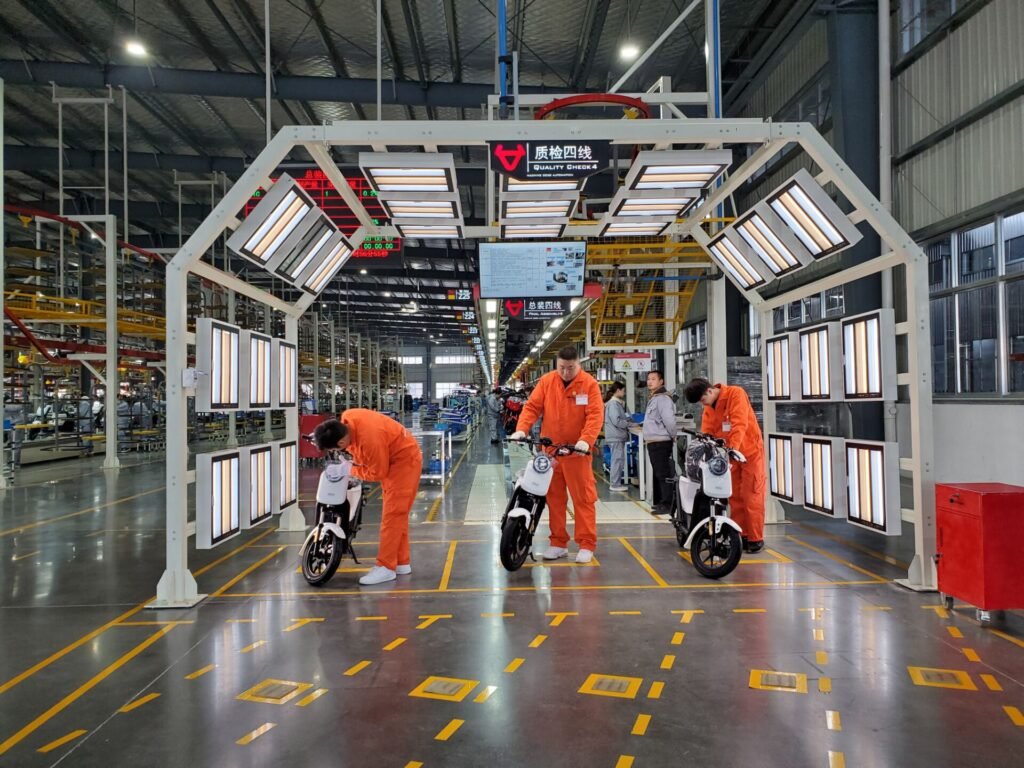
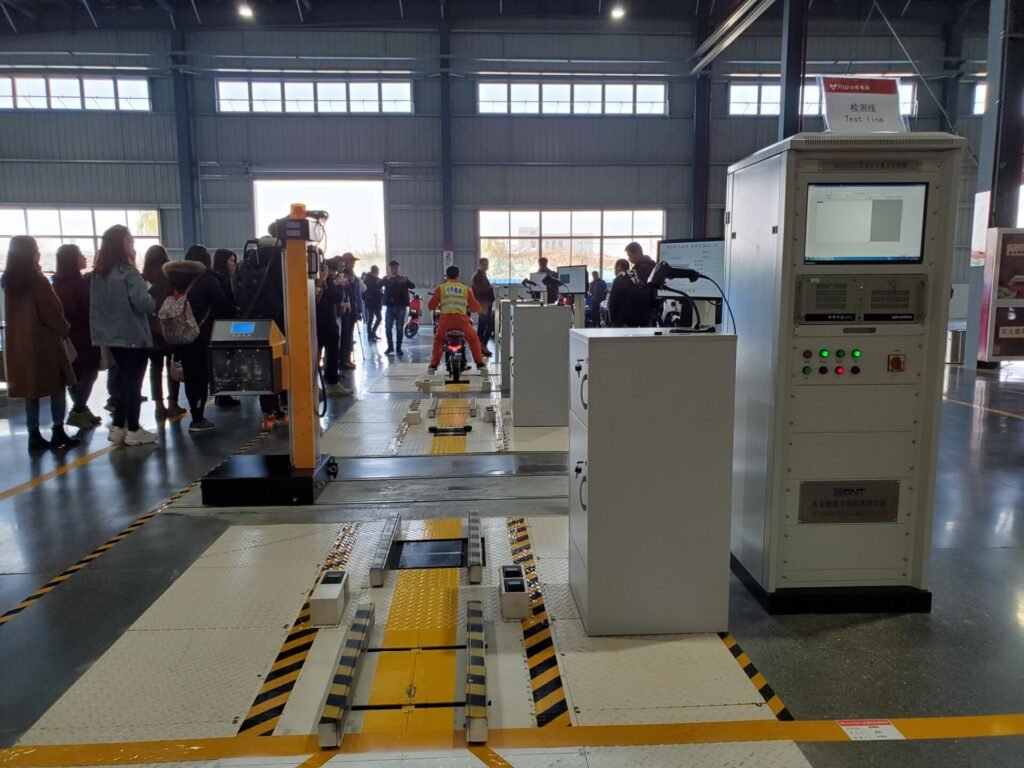
The number of electric scooters that a production line can produce per day depends on a variety of factors, including:
- Designed Capacity of the Production Line: The design of the production line is usually based on the expected maximum production capacity.
- Work Shifts: Whether the production line operates on a single shift or multiple shifts, and the working hours per shift.
- Number and Skill Level of Workers: The number of workers operating the production line and their proficiency levels.
- Level of Automation: Automated equipment and robots on the production line can increase production speed and efficiency.
- Component Supply: The availability of parts, including any shortages or delays.
- Quality Control: The quality inspection process can affect production speed as time is needed to check each vehicle.
- Production Complexity: The complexity of the electric scooter models and configurations being produced also affects the production rate.
- Maintenance and Downtime: Maintenance schedules and unexpected downtime for the production line.
- Production Efficiency: Efficiency in the production process, including waste reduction and process optimization.
Typically, an efficient electric scooter production line can produce between 200 to 500 electric scooters in a single shift (8-hour workday). If operating on two shifts, this number could potentially double or triple.