Maintenance Care and Consumables of Laser Cutting Machines
Proper maintenance and management of consumables are crucial for the efficient operation and longevity of laser cutting machines. Daily checks include inspecting gas pressures, cleaning the cutting head and mirrors, and draining wastewater from the air compressor. Weekly tasks involve clearing exhaust ports and gas line filters. In-depth maintenance, conducted every six months, focuses on cleaning the laser resonator and replacing critical components like vacuum pump oil. The cooling system should also be regularly serviced to ensure optimal performance. Common consumables such as protective lenses, nozzles, ceramic rings, filter elements, auxiliary gases, and coolant need to be replaced based on usage and contamination levels. By adhering to these maintenance practices and managing consumables effectively, laser cutting machines can achieve higher cutting quality, reduced downtime, and extended service life, ultimately enhancing overall productivity and cost-effectiveness.
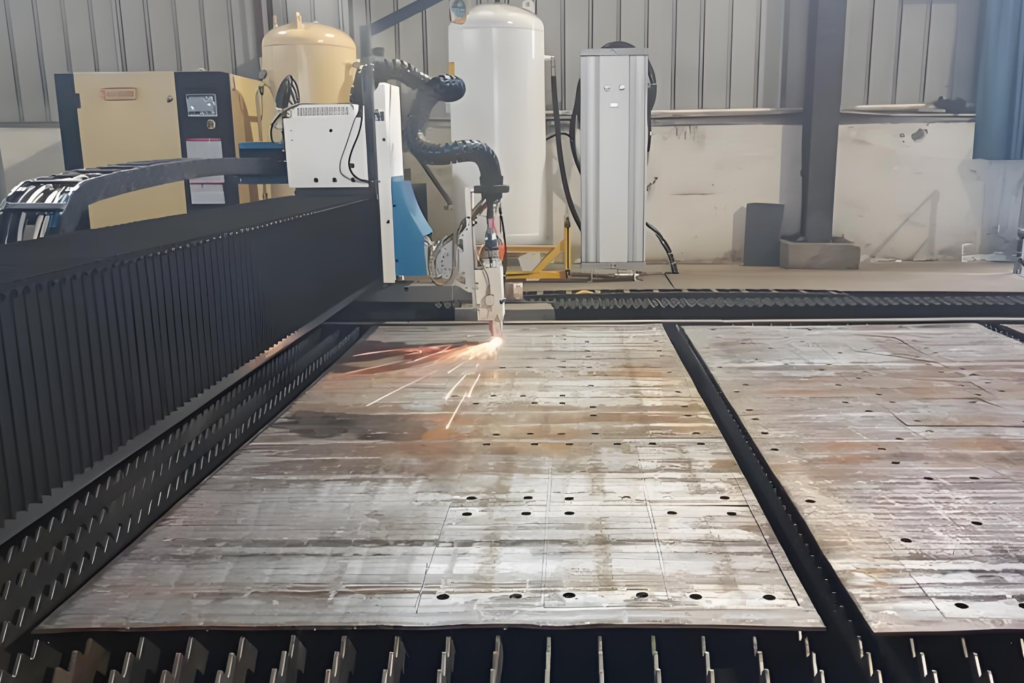
Component | Function Description |
---|---|
Laser Generator | Produces high-energy laser beams, serving as the core power source for cutting. |
Optical System | Includes mirrors and focusing lenses that guide and focus the laser beam to ensure precise energy delivery to the cutting area. |
Cutting Head | Installed at the machine’s end-effector, equipped with a nozzle for ejecting auxiliary gas to facilitate material cutting and melting. |
CNC System | Controls the motion path, cutting speed, and power of the laser cutting machine to ensure precision and efficiency. |
Worktable | Secures and supports the material to be processed. Some worktables enable automated loading and unloading to enhance productivity. |
Cooling System | Provides cooling for the laser generator and optical components to prevent overheating, extend service life, and ensure stable operation. |
Gas Supply System | Supplies auxiliary gases (such as oxygen or nitrogen) for oxidation reactions or slag removal during the cutting process. |
Exhaust System | Absorbs smoke and dust generated during cutting to maintain a clean working environment and protect the health of operators. |
Maintenance and Consumables for Laser Cutting Machines
Maintenance
- Daily Checks and Maintenance
- Check the working gas pressure of the laser and the cutting gas. Replace if insufficient.
- Inspect the zero points and limit switches of the X, Y, and Z axes, as well as the coolant level to ensure no abnormalities.
- Clean the cutting head, mirrors, and nozzles to prevent dust and dirt accumulation.
- Drain the wastewater from the air compressor’s storage tank.
- Clear cutting debris to maintain a tidy workspace.
- Weekly and Periodic Maintenance
- Clean the dust and debris from the exhaust port to ensure proper ventilation.
- Check the gas line filters and remove any accumulated water or debris.
- Clean the ventilation fan filter in the electrical control cabinet to ensure good airflow.
- Regular In-depth Maintenance
- Every six months, inspect the laser cooling water pipes, excitation power supply oil tank, and high-voltage cables.
- Clean the interior of the laser resonator and all mirrors, and readjust the laser output mode.
- Replace the vacuum pump oil and Roots blower oil.
- Cooling System Maintenance
- Regularly replace the coolant and clean the cooling system.
- Check the operation of the chiller unit, and contact a professional for repairs if necessary.
- Other Considerations
- Regularly calibrate the laser output power and beam quality.
- Update the equipment control software to ensure performance and stability.
- Maintain a log of maintenance activities, recording the content and timing of each service.
Common Consumables
Consumable | Function | Replacement Cycle |
---|---|---|
Protective Lens | Focuses the laser beam and protects internal optical paths and core components. | Replace when contaminated or worn |
Nozzle | Ejects auxiliary gas, affecting cutting quality. | Replace periodically based on processing requirements |
Ceramic Ring | Provides electrical signal stability and prevents equipment failure. | Replace when faulty |
Filter Element | Filters impurities and ions from the coolant to extend laser life. | Replace regularly (approximately every 6 months) |
Auxiliary Gas | Used in the cutting process; different gases required for different materials. | Supplement or replace as needed |
Coolant | Cools the laser generator and cutting head. | Replace regularly (approximately every 3 months) |
By following standardized maintenance procedures and using consumables appropriately, the service life of laser cutting machines can be effectively extended, enhancing the stability and cutting quality of the equipment.