Industrial Robot Laser Welding Workstation Design
The design of an industrial robot laser welding workstation focuses on safety, flexibility, high automation, precision, ease of maintenance, and cost-effectiveness. It includes a multi-joint robot, advanced control system, sensors, and fixtures to ensure stable welding quality and efficient production. Safety features like protective enclosures and emergency stops are essential. Modular components and standardized parts facilitate scalability and maintenance. This workstation significantly improves welding efficiency and quality while ensuring operator safety, making it suitable for various industrial applications.
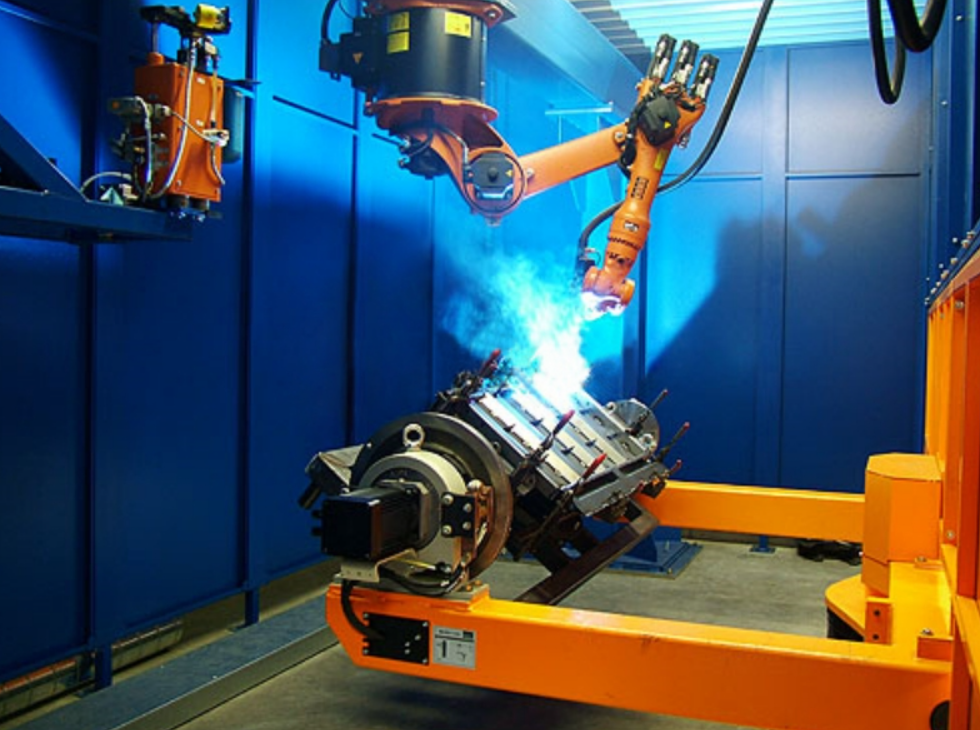
1. Design Principles
- Safety and Reliability: The workstation must comply with national and industry safety standards, equipped with laser protection devices, emergency stop buttons, safety fencing, and other safety features to ensure the safety of operators.
- Flexibility and Scalability: The workstation should be capable of adapting to welding requirements for different materials, shapes, and sizes. Modular design should be adopted to facilitate future functional expansions.
- High Automation: Through path planning, automatic compensation of welding parameters, real-time monitoring, and other technologies, the workstation can achieve automated welding with minimal human intervention.
- High Precision and Welding Quality: Equipped with advanced sensors and vision systems to monitor the welding process in real-time, ensuring the quality and stability of the weld seams.
- Ease of Maintenance and Operation: Standardized components should be used, and detailed maintenance manuals and operating guidelines should be provided to reduce maintenance difficulties.
- Cost-effectiveness: Under the premise of meeting performance requirements, equipment selection and material choices should be optimized to control costs.
2. System Composition
- Robot Body: A multi-joint industrial robot with high precision, high repeatability, and good load capacity should be selected.
- Control System: A high-performance industrial controller should be used, combined with advanced motion control algorithms to achieve precise control of the robot.
- Sensors and Monitoring Systems: Laser rangefinders, vision detection systems, and other devices should be equipped to monitor the position, speed, posture, and other information during the welding process in real-time.
- Welding Equipment and Tools: Select appropriate laser welding machines, welding wires, fixtures, and other auxiliary tools based on welding requirements.
- Fixtures and Positioning Systems: Design dedicated fixtures to ensure the stability of the workpiece during the welding process.
3. Fixture Design
Fixtures are an essential part of the welding workstation, directly affecting welding efficiency and quality. For example, dual fixtures can enable rapid workpiece replacement, improving production efficiency.
4. Positioner Design
Positioners are used to rotate and adjust the position of the workpiece, enhancing welding efficiency. For example, a three-axis vertical tilting positioner can allow for loading and unloading operations while the robot is welding.
5. Control System Design
The control system is the “brain” of the workstation, responsible for coordinating the operation of the robot, fixtures, sensors, and other equipment. PLC and touch screens should be used to achieve centralized control and intelligent operation.
6. Safety Protection Design
Safety protection is an indispensable part of the design. The workstation should be equipped with safety light curtains, protective enclosures, and other facilities to ensure the safety of operators.
7. Case Reference
A company designed a welding workstation that combines a multi-joint robot, laser welding machine, and three-axis positioner to achieve automated welding of air receiver tanks and accessories, significantly improving production efficiency and welding quality.
8. Summary
The design of an industrial robot laser welding workstation requires a comprehensive consideration of various factors. By reasonably selecting equipment, optimizing layout, and control systems, the workstation can achieve efficient and high-quality welding production. At the same time, safety and ease of maintenance are also important aspects that cannot be ignored in the design.
Component | Function Description |
---|---|
Robot Body | The core device for executing welding tasks, with multi-degree-of-freedom motion capabilities to perform precise welding operations along predefined paths. |
Laser Welding System | Provides high-energy-density laser beams for efficient and high-quality welding. |
Control System | Controls the operation of the robot and welding equipment, including path planning, welding parameter settings, and real-time monitoring, to ensure automated and precise welding processes. |
Sensor System | Includes vision sensors, laser rangefinders, etc., to monitor welding positions and seam quality in real-time, enabling dynamic adjustments during the welding process. |
Fixtures | Used to secure workpieces, ensuring stability during welding to improve welding precision and efficiency. |
Positioner | Adjusts the position and angle of the workpiece to facilitate easier access for the welding robot, enhancing welding efficiency and flexibility. |
Safety Devices | Includes protective enclosures, safety light curtains, emergency stop buttons, etc., to protect operators from laser radiation and mechanical hazards, ensuring safe operation of the workstation. |
Auxiliary Equipment | Includes dust extraction systems, cooling systems, etc., to improve the working environment, extend equipment lifespan, and ensure welding quality. |
The installation methods of industrial robots in welding applications are mainly as follows. Each method is chosen based on actual production needs and space conditions:
- Upright Installation
The robot is directly fixed on the ground or installed with a base. This method is simple, stable, and reliable, and is suitable for various industrial scenarios such as welding, loading and unloading, and handling. - Guide Rail Walking Seventh Axis Installation
On the basis of upright installation, a ground moving guide rail is added, allowing the robot to move left and right, expanding its working range. This is suitable for welding longer workpieces or multi-process operations. - Suspended Installation
The robot is hung upside down from the ceiling or a支架. This method is suitable for scenes with limited space or tasks that need to be performed at a height, such as welding large workpieces or spray painting. - Suspended Mobile Installation
Combining suspended installation and guide rail walking, the robot moves along the guide rail, further expanding its working range. This is suitable for scenarios with high space utilization requirements. - Wall-mounted Installation
The robot is installed on a wall, suitable for tasks in the vertical direction, saving space. - Inclined Installation
Suitable for tasks that need to be performed on an inclined surface. - Custom Installation
Designed specifically according to production needs, such as installation inside a machine tool or fixed on a machine table, to meet special process or space requirements.
When choosing an installation method, it is necessary to consider the task requirements, space conditions, safety, and stability comprehensively to ensure that the robot runs efficiently and stably on the production line.