Automated Production Line for Laser Welding of Flat Wire Motors
The automated production line for laser welding of flat wire motor stators is designed to achieve high efficiency and precision. The process begins with accurate weld point positioning using cameras and OCT detection modules, followed by optimized laser scanning trajectories tailored to the dimensions and connection directions of flat copper wires. High-speed galvanometers and disk lasers ensure efficient and high-quality welding, while vision systems monitor and inspect weld quality in real-time. The line’s automation, driven by six-axis robots, enhances production efficiency and flexibility. Its modular design allows for scalable capacity, and the intelligent process control adapts to various winding forms. This system not only boosts productivity but also reduces environmental impact through energy-efficient laser technology, making it a state-of-the-art solution for modern stator manufacturing.
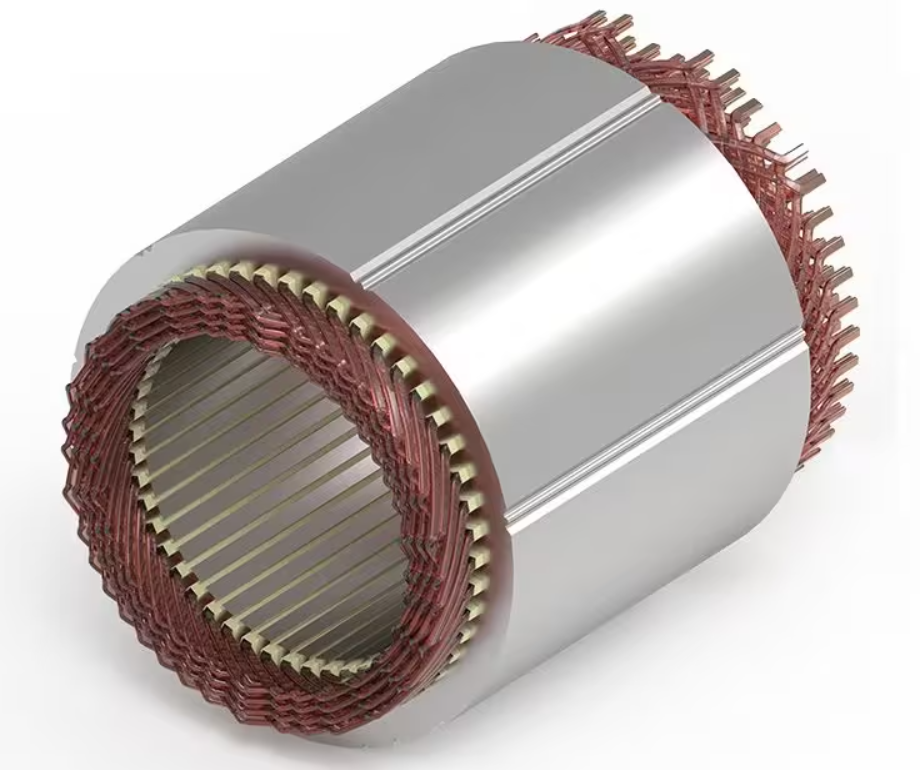
Process Flow of Laser Welding for Flat Wire Motor Stator and Features of the Automated Production Line
Laser Welding Process Flow
- Weld Point Positioning and Detection
Before welding, a camera and OCT detection module installed on the scanning welding head are used to determine the position of the weld point, cross-sectional dimensions, and 3D assembly status. The scanning trajectory dimensions are then fine-tuned based on the gap status information. - Laser Scanning Trajectory Design
The laser scanning trajectory dimensions and number of scans for a single weld point are determined based on the cross-sectional dimensions and connection direction of the flat copper wire. Short-side connections use linear oscillation trajectories, while long-side connections use circular or elliptical oscillation trajectories to reduce spatter and porosity. - Welding Parameter Optimization
Constraints on energy intensity are established to determine the welding time and laser power. High-quality welding is achieved using a large-format scanning galvanometer combined with a ring-shaped laser beam. - Welding Execution
Disk lasers and high-speed optical galvanometers are used for welding, combined with an image capture system for position detection to ensure high precision and efficiency during the welding process. - Weld Point Inspection and Quality Control
After welding, the quality of the weld point is inspected using a vision system to ensure the tensile strength and conductivity of the weld. Real-time monitoring of issues such as light leakage and gaps during the welding process is also conducted.
Features of the Automated Production Line
- High Degree of Automation
The production line utilizes six-axis robots to achieve full automation from stator lifting and pressing, laser welding, demolding, measurement and inspection, to laser marking. - High Welding Quality
Laser welding technology optimizes the welding path and uses vision guidance to reduce spatter and porosity, enhancing the tensile strength and conductivity of the weld points. - High Production Efficiency
Laser welding significantly improves production efficiency compared to traditional welding processes. The modular design of the automated production line can be flexibly expanded based on production capacity requirements. - Intelligent and Flexible
The production line is equipped with a process expert database that can intelligently match the joint status with the welding process, meeting the welding requirements of different winding forms. - Environmentally Friendly and Energy-Efficient
Laser welding reduces waste slag and spatter generated by traditional welding processes while lowering energy consumption.
By integrating the above process flow and production line features, the automated production line for laser welding of flat wire motor stators can significantly enhance production efficiency and product quality while reducing production costs and environmental impact.