Design and Manufacture of Laser Welding Equipment for Automotive Components
The design and manufacture of laser welding equipment for automotive components involve creating a mobile support structure with clamping mechanisms and integrating a welding head with robotic arms for flexibility. Technical parameters such as laser power (50W–4kW), welding speed (0.1–10m/min), weld width and depth (0.1–5mm), and precision (±0.1–±0.5mm) are carefully set. The equipment is used for welding automotive bodies, structural components, powertrain parts, and new energy vehicle components. High-precision machining and automated assembly ensure reliability. Parameter optimization and protective gas systems enhance welding quality. The equipment supports lightweight and high-strength applications, contributing to vehicle safety and efficiency.
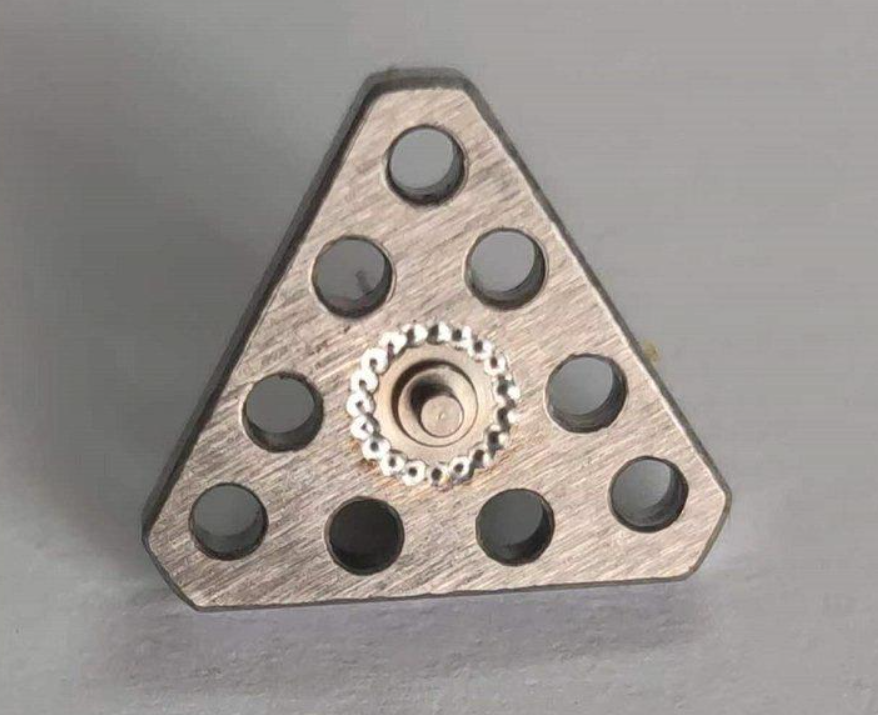
Design and Manufacture of Laser Welding Equipment for Automotive Components
I. Design
- Equipment Structure Design:
- Mobile Support Mechanism: It includes a support base and four clamping and fixing mechanisms, with mobile cushioning mechanisms evenly distributed around the bottom.
- Welding Head Integration: The laser welding equipment typically integrates the welding head with a robotic arm for flexible operation.
- Technical Parameter Design:
- Laser Power: The power range is generally from 50W to 4kW, depending on the thickness and type of the welding material.
- Welding Speed: The speed range is from 0.1m/min to 10m/min.
- Weld Width and Depth: The width and depth are usually between 0.1mm and 5mm.
- Welding Precision: The precision range is from ±0.1mm to ±0.5mm.
- Defocusing Amount: Positive and negative defocusing are adjustable, with negative defocusing providing greater penetration depth.
- Pulse Parameters: Pulse duration, frequency, and peak power are adjustable, with short pulses suitable for small and complex welding.
II. Manufacture
- Manufacturing Process:
- High-Precision Machining: Ensuring the precision of the welding head and mobile support mechanism.
- Automated Assembly: Enhancing the stability and reliability of the equipment.
- Equipment Commissioning:
- Parameter Optimization: Adjusting laser power, welding speed, and other parameters according to actual welding requirements.
- Protective Gas System: Using inert gases to expel plasma and protect welding quality.
III. Technical Parameter Table
Parameter | Unit | Value Range | Notes |
---|---|---|---|
Laser Power | W | 50-4000 | Adjusted according to the thickness and type of welding material |
Welding Speed | m/min | 0.1-10 | Adjusted according to the welding material and plan |
Weld Width | mm | 0.1-5 | Adjusted according to the welding material and plan |
Welding Depth | mm | 0.1-5 | Adjusted according to the welding material and plan |
Welding Precision | mm | ±0.1-±0.5 | Adjusted according to the welding material and plan |
Defocusing Amount | mm | Adjustable positive and negative | Negative defocusing provides greater penetration depth |
Pulse Width | ms | Adjusted according to material | Short pulses are suitable for small and complex welding |
IV. Application
- Automotive Body Welding: Used for welding different parts of the body, such as the trunk lid, door inner panel, etc.
- Body Laser Assembly Welding: Used for welding sub-assemblies or assemblies of the white body to increase body stiffness.
- Typical Components: Such as intake and exhaust valves, clutches, bumpers, etc., to meet the requirements of high strength and lightweight.
- New Energy Vehicle Key Components: Precision welding of battery packs and air outlets to meet the requirements of lightweight and high strength.
V. Application Scope Table
Application Scope | Specific Use |
---|---|
Automotive Body | Laser welding of roof, trunk lid, frame, etc. |
Body Structural Components | Laser welding of doors, body side frames, pillars, etc. |
Variable Thickness Laser Welded Blanks | Used for body side frames, door inner panels, windshield frames, wheel arch panels, floor panels, center pillars, etc. |
Powertrain Components | Welding of drive shafts, exhaust pipes, etc. |
New Energy Vehicle Components | Welding of batteries and air outlets, sensors and electronic units, etc. |
Other Components | High-voltage relays, filters, torque sensors, turbochargers, fuel rails, cylinder gaskets, spark plugs, segmented motor stators, seat adjustment screws, airbags, etc. |
VI. Development Trends
- Automation and Intelligence: Using computer control and robotic technology to improve production efficiency and welding quality.
- High Precision and High Efficiency: Continuously optimizing welding process parameters to enhance equipment performance.
- Lightweight and High Strength: Reducing vehicle weight and improving the integration and safety performance of the body through laser welding technology.