Motorcycle Frame Robotic Welding Production line
The industrial robot automated welding production line for motorcycle frames is a highly efficient solution that integrates welding robots, positioners, fixtures, and automated conveyance systems. It employs advanced welding techniques such as MAG or CO₂ welding, ensuring high precision and consistent quality. The system is controlled by a centralized PLC, enabling seamless coordination among components. This setup significantly boosts production efficiency by up to 50%, reduces labor intensity, and enhances welding quality with a pass rate of over 97%. Safety features like protective fencing and emergency stops ensure a secure working environment. The flexible design allows for easy adaptation to different frame models, making it a vital component in modern motorcycle manufacturing.
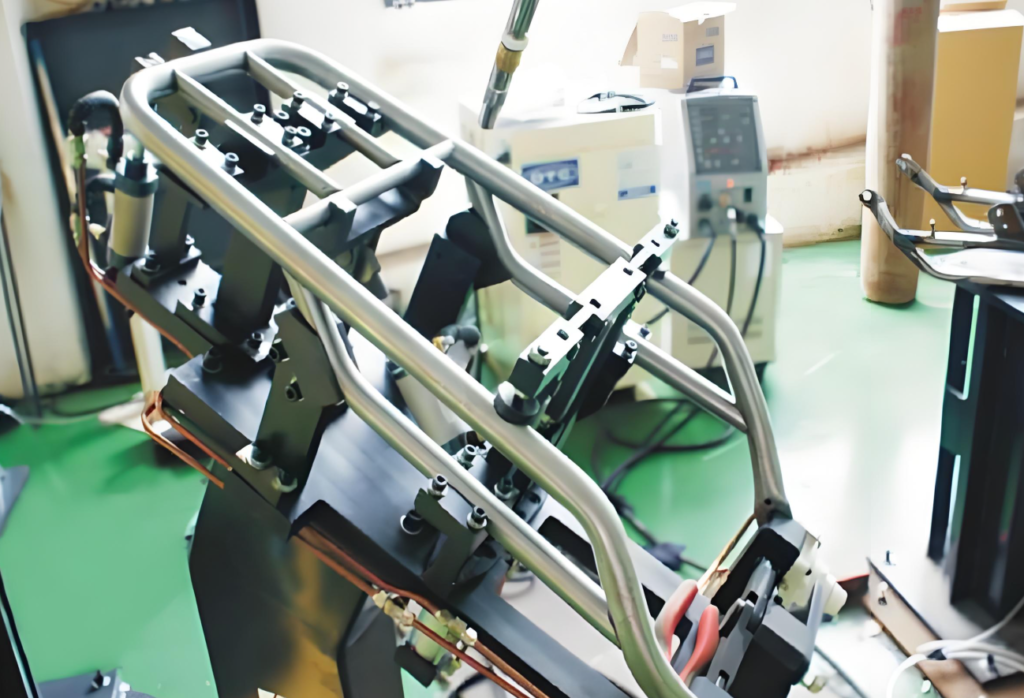
Industrial Robot Automated Welding Production Line for Motorcycle Frames
The industrial robot automated welding production line for motorcycle frames is a highly efficient and precise manufacturing solution widely used in modern motorcycle production. Below is a detailed introduction to this production line:
1. Components of the Production Line
- Welding Robots: The production line is equipped with multiple welding robots that perform welding tasks. These robots can follow predefined welding paths and parameters to ensure consistent and high-quality welding.
- Positioners and Fixtures: Positioners adjust the position and angle of the motorcycle frame to facilitate welding by the robots. Fixtures are used to secure the frame during the welding process to ensure stability.
- Automated Conveyance System: Automated transporters or conveyors move the frames and components to the welding stations, enabling unmanned production.
- Control System: A PLC controller or advanced automation control system centrally manages the robots, positioners, and conveyance systems.
2. Welding Processes and Techniques
- Welding Methods: Motorcycle frame welding typically employs MAG welding or CO₂ shielded arc welding, which are suitable for various welding requirements.
- Welding Parameters: Parameters such as welding current, voltage, gas flow, and welding speed are adjusted according to the material and thickness of the frame. For example, in MAG welding, the current is set to 110–130 A, voltage to 14–17 V, and welding speed to 15–22 cm/min.
- Quality Inspection: After welding, non-destructive testing techniques are used to inspect the weld seams to ensure their strength and sealability.
3. Advantages and Benefits
- Increased Production Efficiency: The automated welding production line significantly improves production efficiency, with a capacity increase of 50%.
- Enhanced Welding Quality: The robotic welding process produces higher-quality and more aesthetically pleasing weld seams, with a quality pass rate increasing from 70% to 97%.
- Reduced Labor Intensity: The automated production line reduces manual operations, lowering the physical demands on workers.
4. Production Line Configuration Chart
Equipment Name | Function Description | Quantity |
---|---|---|
Welding Robots | Execute welding tasks with multi-axis motion capabilities to complete complex welding paths | 4 units |
Positioners | Adjust the position and angle of the frame to expand the welding range of the robots | 2 units |
Fixtures | Secure the frame to ensure stability during the welding process | 8 sets |
Automated Conveyance System | Automated transporters or conveyors for the automated movement of frames and components | 1 set |
Control System | Centrally control robots, positioners, and conveyance systems to achieve automated production | 1 set |
Welding Power Supply | Provide stable welding current and voltage, supporting MAG/CO₂ welding | 4 units |
Safety Devices | Including protective fencing, emergency stop buttons, safety light curtains, etc., to ensure operational safety | 1 set |
Auxiliary Equipment | Including dust extraction systems, cooling systems, etc., to improve the working environment and extend equipment life | 1 set |
5. Case Study
A motorcycle manufacturing company introduced an automated robotic welding production line, achieving high-efficiency and high-quality frame welding. The production cycle for each frame is less than 100 seconds, with significant improvements in welding quality and a 42.8% increase in production efficiency.
In summary, the industrial robot automated welding production line for motorcycle frames not only improves production efficiency and welding quality but also reduces production costs and labor intensity. It is an essential manufacturing solution in modern motorcycle production.