Robotic Welding Production Line for Framework Structural Components
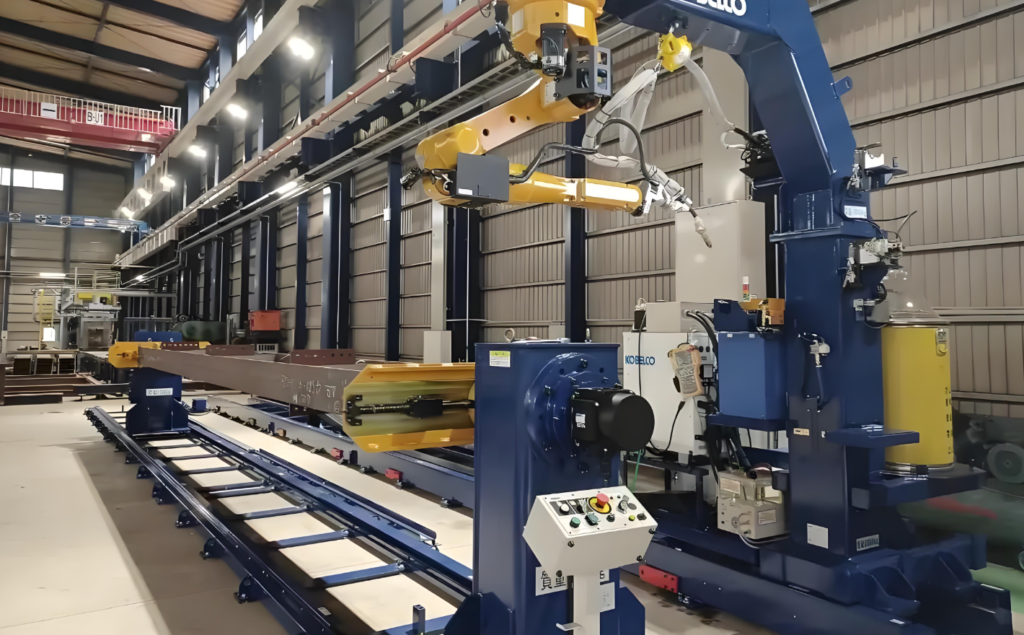
Robotic Welding Production Line for Framework Structural Components
A robotic welding production line for framework structural components is a highly automated and intelligent manufacturing system widely used in industries such as construction, machinery manufacturing, and automotive. Below is a detailed description of this production line:
1. Components of the Production Line
- Welding Robots: The core equipment of the production line, typically using multi-joint six-axis industrial robots capable of performing complex welding paths.
- Welding Equipment: Including welding power supplies, wire feeders, welding torches, etc., supporting various welding processes.
- Positioners and Fixtures: Used to secure and adjust the position of workpieces to ensure welding accuracy.
- Control System: Utilizing PLC and robot control systems to achieve automated production.
- Logistics System: Including conveyors, RGV vehicles, etc., for automated transportation of workpieces.
- Inspection System: Equipped with vision sensors, laser positioning devices, and other equipment to monitor welding quality in real-time.
2. Process Flow
- Material Preparation and Cutting: CNC cutting technology is used to ensure the dimensional accuracy of components.
- Assembly and Welding: Workpieces are secured by fixtures, and robots perform welding according to predefined paths.
- Quality Inspection: After welding, vision inspection systems are used to check the quality of the weld seams.
- Logistics Transfer: Finished products are transported to the next process via an automated logistics system.
3. Technical Parameters
No. | Item | Requirement |
---|---|---|
1 | Working height of the production line | 700-900 mm |
2 | Production cycle per component | ≤ 8 hours |
3 | Number of workers per component | ≤ 10 persons |
4 | Number of six-axis robots | 1–100 sets |
5 | Welding torch cooling method | Water-cooled |
6 | Welding positioning method | Contact and arc sensors |
7 | Welding tracking method | Arc tracking |
4. Design Highlights
- High Degree of Automation: The production line achieves an automation rate of over 90%, reducing manual intervention.
- Flexible Production: Supports mixed-line production of various structural components.
- Smart Monitoring: Equipped with electronic dashboards and MES systems to enable full traceability of the production process.
- Efficient Logistics: Utilizes RGV vehicles and roller conveyors to improve transfer efficiency.
5. Case Study
After adopting this production line, a company achieved 24/7 continuous production. Welding quality was significantly improved, and production efficiency was increased by four times.
This production line is a highly efficient and intelligent solution that enhances welding quality and production efficiency, making it an essential choice for modern industrial manufacturing.